Environmental Challenges to Manage When Constructing High-Tech Manufacturing Facilities
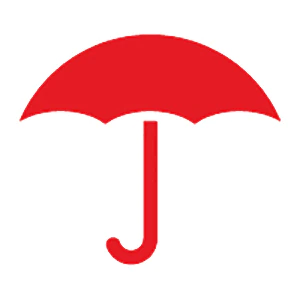
The expansion of high-tech manufacturing across the United States means more opportunities for contractors who can build specialized facilities to house sophisticated operations. However, significant environmental risks may add to the inherent complexity of constructing large and technically advanced structures. Working with and around potentially hazardous materials, equipment and waste requires adherence to strict codes, regulations and specifications, as well as specialized knowledge, skills and experience.
Factors that could increase pollution hazards on high-tech manufacturing construction projects.
Inexperience and knowledge gaps
For contractors, branching out to high-tech construction may require training in the proper handling of hazardous materials and waste disposal, as well as proficiency in the relevant building codes, techniques and sustainability practices. From soil and groundwater contaminated by spills, leaks or seepage, to injuries due to contact with toxic chemicals, particulates or fumes, any failure to identify or properly mitigate environmental exposures could result in a pollution liability claim.
Project complexity
Environmental issues at high-tech facilities are sometimes traced back to failures when interpreting or implementing complex design drawings and specifications. Starting work before properly addressing questions or concerns about the project plan, including the potential environmental impact, could ultimately leave contractors at risk for pollution liability. Understanding project requirements and getting the appropriate sign-offs on any deviations from initial designs – such as product or material substitutions, recommended building or installation techniques, equipment used and other value engineering decisions that were made – may help offset these risks.
Imperfect facility site conditions
Whether breaking new ground, constructing over an abandoned lot or expanding the footprint of an existing structure, one of the greatest risks of a high-tech build can be from the facility grounds. Even if a contractor is not involved in the site selection process, they could be held liable for environmental impacts and non-compliance resulting from unknown or unintentional ecosystem disruptions or legacy pollution. Responsibility to remediate preexisting environmental conditions and help prevent new ones, as well as reduce the impact on surrounding habitats and communities, could fall to the contractor. If unaware or unprepared, the contractor may be at risk of liability.
Hazardous materials and waste handling, storage and disposal
Asbestos, adhesives, diesel fuels, flame retardants, halogenated compounds, refrigerants, resins, solvents and more – high-tech operations and associated construction activities often necessitate working around or coming into contact with hazardous materials and potentially harmful waste. Contractors face unique environmental challenges in building, installing or utilizing structures and systems to store, contain or transport and dispose of hazardous substances and waste used in the construction of high-tech facilities. Completing projects in ways that limit exposures to hazardous materials, both during and after construction, is key to minimizing risk.
Deficiencies in commissioning process
Environmental exposures often come to light in the critical final stages of a high-tech manufacturing facility build. Careful planning and execution of commissioning and turnover activities – including participation in or oversight of the first production run – can help prevent costly setbacks. Testing and verifying that the build went according to plan and demonstrating that your team properly disposed of waste, handled hazardous materials conscientiously and followed regulations diligently throughout construction may help minimize liability for remediation or environmental damage, among other things.
Proactive project planning and management can help minimize high-tech environmental risks.
Environmental challenges in the construction of high-tech manufacturing facilities can vary greatly depending on the nature of the structure, the construction processes, the materials and equipment used and the existing environmental conditions at the building site. Following these key best practices can support mitigating risks related to environmental exposures on high-tech builds.
- Select projects carefully, evaluating each opportunity to ensure it involves teams with a proven track record in delivering high-tech projects with minimal environmental impact.
- Participate in project planning discussions, particularly those addressing the potential environmental impact of the project, including construction materials or methods.
- Diligently monitor project teams and progress to support compliance efforts with environmental regulations, design specifications, safety data sheets, safe handling guidelines and waste management requirements.
- Keep and retain records, including change orders and sign-offs, official inspection reports, material safety and equipment-operating manuals, and evidence of adherence to environmental safety standards.
- Follow rigorous quality assurance and control practices, such as inspecting materials prior to installation, using third parties to test and validate environmental compliance or deploying technology to help identify and address potential environmental issues.
- Use contracts to effectively transfer risk, ensuring that each includes clearly defined liability, subrogation, indemnification or hold harmless clauses and environmental compliance requirements and responsibilities. Discuss appropriate pollution liability limits and coverages with your agent and an attorney familiar with these unique exposures.
High-tech builds demand high-quality insurance solutions.
Comprehensive coverage from a carrier with experience and expertise helping to mitigate environmental challenges can be one of the most powerful tools on a high-tech construction job. For example, Travelers works collaboratively with contractors to help minimize environmental risks that can lead to bodily injury, property damage, pollution cleanup costs and claims for other potential liability. By doing so, companies can focus on capitalizing on high-tech opportunities and growing their business.
Standard Commercial General Liability policies exclude coverage for most pollution claims, but Travelers supports contractors with industry-leading ECP CustomSM Contractors Pollution Liability insurance coverage and dedicated risk control specialists who support clients through guidance and consultation on environmental hazards and related best practices.
To learn more about Travelers innovative insurance and risk management solutions for construction companies, contact your agent.