Manage Construction Defect Risks When Building High-Tech Facilities
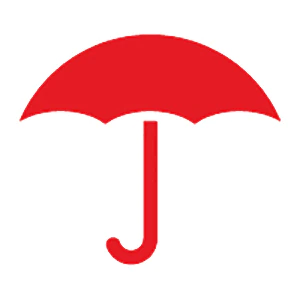
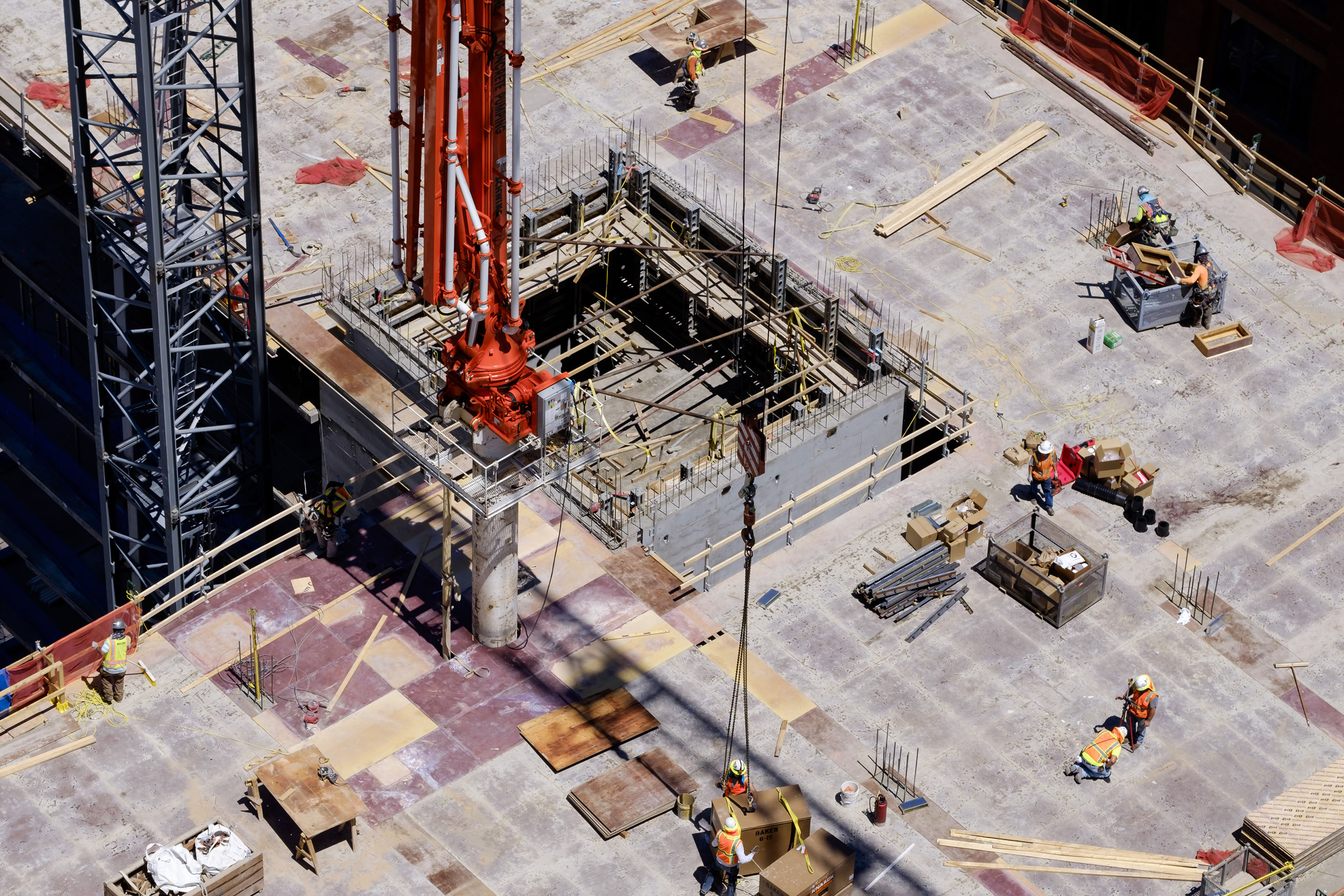
From clean energy components and semiconductors to the end products in which they’re used, U.S. ambitions to increase onshore high-tech manufacturing is growing.
The more sophisticated the build is, the more risk there may be. Strict technical specifications, stringent building codes and specialized labor involved in building multibillion-dollar, high-tech manufacturing plants can add layers of intricacy and interdependency. Just one mistake, miscommunication or miscalculation could lead to a construction defect claim.
Mitigate these construction defect risks on high-tech manufacturing facility builds.
Design misinterpretations and value-engineering changes
Construction defects that trace back to design issues can be amplified on high-tech manufacturing facility projects. The engineering of these massive, highly sophisticated facilities often requires collaboration between unusually large, specialized design teams, with in-house resources and third-party firms each handling specific aspects of the project plan. Some design teams may even be in other countries. Misinterpretations or mismanagement of the design and construction process – including any value engineering changes made along the way – can lead to critical flaws that contractors could be held liable for down the road if they were involved in any part of the design.
Tight tolerances and intricate integrations
Unlike other types of buildings, high-tech facilities may have to adhere to precise construction tolerances to ensure optimal operational efficiency. They may also require the intricate integration of sophisticated, sensitive, often automated equipment, systems and environmental controls to maintain desired operating conditions. Even the slightest deviation from specifications for floor levelness, temperature control, air pressurization, vibration absorption and more – including any technologies installed to regulate these variables – could cause issues with plant or product performance that might lead to construction defect claims.
Product or material availability and failures
Due to their complex operational requirements, high-tech manufacturing facilities are often designed with specific products and materials in mind. Extenuating circumstances – from unexpected supply chain disruptions to unforeseen compatibility issues – can create barriers to obtaining the required resources. Projects stalled by material availability or performance problems can put timelines and budgets at risk, and pressure to keep on track often requires making quick decisions about using backup suppliers and alternate or modified materials. Failure to thoroughly evaluate the quality, reliability and integrity of replacement vendors, products or materials prior to procurement or installation can have serious impacts on facility performance and safety, potentially increasing construction defect risk.
Workforce shortfalls and language barriers
High-tech builds could also require large teams with specialized skills. Since large-scale construction of advanced manufacturing facilities is gaining momentum in the U.S., qualified workers with training and experience in the techniques, equipment and materials required to meet the design requirements for these buildings can be hard to find, attract and retain. Careful communication and coordination between independently operating designers, engineers, contractors and laborers on the project team is crucial but may be difficult to manage and maintain. Furthermore, project stakeholders may not have extensive experience building on American soil, so language and cultural barriers, lack of familiarity with domestic building codes and techniques, and architectural designs translated to English can complicate builds. Such challenges may make it more difficult to successfully collaborate, construct and deliver projects according to plan.
Insufficient commissioning and turnover
From ensuring that a project meets the design and code requirements to training building operations and maintenance staff, the final stages of a high-tech manufacturing facility build can be the most critical to its success. Without careful planning and execution, defects or deficiencies discovered during the testing and verification process may be more difficult, timely and expensive to resolve. More important, if building owners and operators do not receive comprehensive documentation and instruction on how to properly run and maintain the facility, post-turnover, architectural, structural or mechanical malfunctions could come back as construction defect claims, which can be complicated and costly.
Comprehensive risk management is critical to help mitigate construction defect risk on high-tech manufacturing builds.
From pre-planning to post-delivery, taking the necessary precautions to help prevent or minimize the potential impact of structural and system failures can help ensure your final build is free of critical flaws that could be traced to a construction defect.
Incorporate key risk management strategies and best practices.
- Diligent project selection, planning and management. Establish and maintain clear lines of communication among key stakeholders, suppliers, owners, designers, subcontractors and team members through every phase of the build.
- Meticulous, ongoing project documentation. Create and retain critical records – from receipts for expenses incurred and copies of subcontractor certificates of insurance to photographic evidence of workmanship and sign-off on any value engineering decisions.
- Rigorous quality assurance and control. Carefully inspect products and materials prior to installation. Provide keen oversight of worker qualifications and job performance and third-party or technology-assisted testing and validation of construction quality and building performance.
- Comprehensive contractual risk transfer. Ensure that all contracts with third parties (e.g., subcontractors, vendors and suppliers) address contractual risk transfer and spell out indemnification and insurance requirements. These contracts should also clearly define project scope, schedule, budget, team responsibilities, insurance and license requirements, as well as procedures for submitting and approving change orders.
Partner with a trusted insurance provider to help mitigate construction defect risk.
Choose a carrier that has specialized coverage and deep experience in construction. Travelers has dedicated construction claim investigation specialists and a state-of-the-art forensics lab. Travelers’ industry-leading risk management solutions and services are designed to help protect contractors from the potentially devastating impact of a construction defect claim. Deep subject matter expertise coupled with advanced incident analysis to identify emerging issues and trends driving the frequency and severity of construction losses is a key differentiator. Get comprehensive, customized coverage and consultation to help mitigate construction defect risks.
To learn more about Travelers innovative insurance and risk management solutions for construction companies, contact your agent.