6 Top Manufacturing Technology Trends: The Benefits and Risks
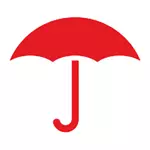
(SPEECH)
[MUSIC PLAYING]
(DESCRIPTION)
The Travelers red umbrella logo appears in the center of the screen.
Text, the human side of advanced manufacturing.
Scenes of illuminated sensors and robotic machines as they manufacture products.
Chris Hayes, AVP Risk Control, Workers Compensation and Transportation.
(SPEECH)
CHRIS HAYES: Smart sensors, robotics, and augmented reality, these are just a few of the advancements that are transforming manufacturing. And as an insurance professional, I know firsthand how these changes are significantly transforming something else, risk.
(DESCRIPTION)
Two people in a factory wear hard hats, protective eye goggles, and safety ear muffs around their necks as they have a conversation and consult a tablet in front of a robotic machine.
Robotic machines move cardboard boxes around a warehouse.
(SPEECH)
From supply chain challenges, to information security, to quality control, implementing digitally driven operations has many risk considerations, including your workforce.
(DESCRIPTION)
A graphic reads, Internet of Things, IOT. Robotics, which shows a robotic arm, data analytics, which shows energy around a canister, augmented slash virtual reality, which shows a person wearing a virtual reality headset, and 3D slash 4D printing, which shows a printer creating something out of a block of material.
Workers wear protective eye goggles, reflective vest, and hardhats, while another person holds a tablet.
(SPEECH)
Evolving jobs, disappearing roles, and learning new skills are among the challenges that employers and employees face.
(DESCRIPTION)
A person gives a talk to large audience.
(SPEECH)
Considering the human side of the equation is one of the best ways to ensure workers adjust, the risks are manageable, and new technologies get off the ground.
(DESCRIPTION)
A person stands in a factory cargo area and programs a drone to deliver a package.
Text, Advanced Manufacturing, Managing the Digital Transformation Journey.
(SPEECH)
And that's why you want to read our new whitepaper, "Advanced Manufacturing-- Managing the Digital Transformation Journey." It's the perfect primer for the future of manufacturing. You'll find it at travelers.com/AdvancedManufacturing.
(DESCRIPTION)
The Travelers red umbrella logo appears in the center of the screen.
Text, download our white paper, Travelers dot com slash Advanced Manufacturing.
This material does not amend, or otherwise affect, the provisions or coverages of any insurance policy or bond issued by Travelers. It is not a representation that coverage does or does not exist for any particular claim or loss under any such policy or bond. Coverage depends on the faces and circumstances involved in the claim or loss, all applicable policy or bond provisions, and any applicable law. Availability of coverage referenced in this document can depend on underwriting qualifications and state regulations.
Copyright 2022, The Travelers Indemnity Company. All rights reserved. Travelers and the Travelers Umbrella logo are registered trademarks of The Travelers Indemnity Company in the U.S. and other countries.
Smart technology is transforming virtually every aspect of manufacturing. Advanced robotics are taking on tasks that once seemed impossible to automate, from picking and packing to gluing, welding and spraying. Embedded sensors can monitor equipment health, enabling predictive maintenance. 3D printing helps manufacturers quickly design and produce products tailored to their customers' unique requirements.
These are just a few of the competitive advantages of smart technology. Many manufacturers are optimistic about the possibilities – and recognize that digital transformation is a marathon and not a sprint. Indeed, understanding the risks and rewards of digital integration is vital to long-term success.
Here's a look at the benefits and risks of top technology trends in manufacturing today.
1. Equipment maintenance
Unplanned downtime due to equipment failure can bring production to a halt. With smart technology, manufacturers can anticipate breakdowns before they occur. Embedded sensors monitor machine performance and track various data points, such as temperature, speed, vibration and lubrication. This vital information provides real-time insights into equipment health and when service and repairs will be required.
Benefit: Rather than wait for a machine to fail, maintenance crews can schedule maintenance and make repairs precisely when they're needed. This may help to reduce downtime and maintenance costs and may increase operational stability.1 Integrated sensors can also help identify problems before they ripple through the entire production line.
Risk: A malfunctioning sensor that fails to trigger a warning may compromise production and the quality of the finished product. For example, a metals manufacturer could be forced to scrap hundreds of cases of finished metal brackets when a sensor fails to detect an out-of-tolerance condition.
2. Inventory and supply chain management
Sensors and location-aware technology allow manufacturers to track parts and supplies on a global scale. For instance, radio frequency identification (RFID) tags can be attached to parts, shipping containers and raw materials to provide real-time delivery status and alert manufacturers of arrival times. Data gathered from multiple sensors can help manufacturers plan inventory, forecast demand and be more responsive to customer needs.
Benefit: With end-to-end visibility over the entire supply chain, manufacturers can use the data from sensors and other tracking devices to:
- Reduce disruption.
- Better manage risk.
- Track down lost or misplaced items.
- Plan inventory and forecast demand.
- Offer customers information on shipping times and potential delays.
- Expedite tracking for product recalls.
Risk: A breakdown in tracking technology may hamper a company's ability to locate products and pull defective items out of the marketplace. This could present a problem in the event of a product recall.
3. Production process and quality control
Technology's biggest impact may be in the areas of production and quality control:
- Digitally integrated software and sensors can identify opportunities to increase productivity and warn of conditions that are detrimental to it.2
- Robots can work tirelessly to complete a range of repetitive tasks – from assembly and welding to product inspection and testing – with consistent results.
- Cameras and machine vision can detect product flaws that may otherwise go unnoticed, taking quality control to a new level.3
- Systems can monitor environmental conditions, such as temperature and humidity, and automatically adjust equipment to keep production flowing smoothly.
Benefit: Removing the human element may bring greater efficiency, accuracy and quality control to the production process. Sensors can capture data at a granular level, allowing greater precision in functions with strict manufacturing standards, such as those enforced by the aerospace and defense industries. Data analytics may reveal ways to streamline production and steer future operations.
Risk: Automated equipment may perform unexpectedly because of human error. For example, if a plant employee loads the wrong solution into a machine, it could result in flawed finished products that sensors may not be able to detect. Manufacturers may want to perform a failure mode and effects analysis (FMEA) to anticipate what could go wrong and incorporate additional quality control processes based on the results.
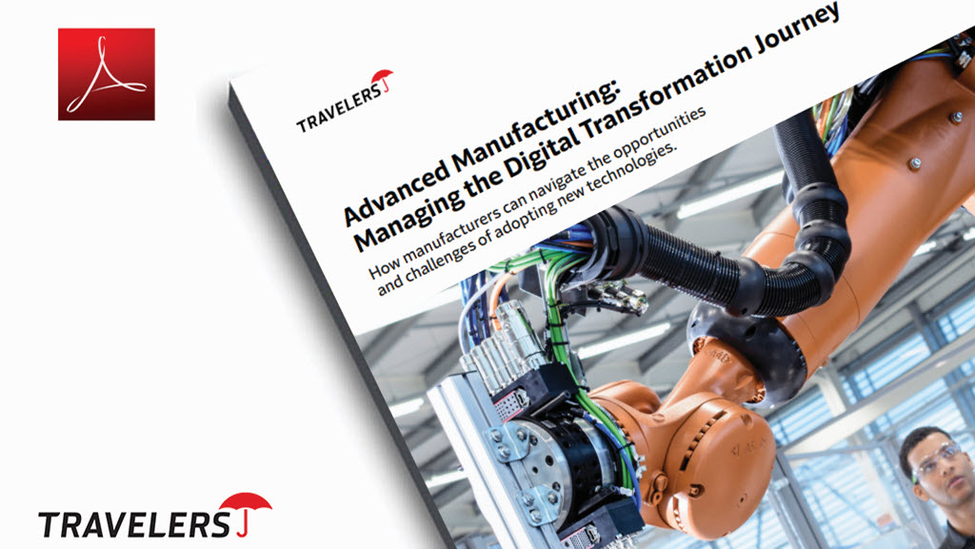
Balancing the Risks of Technology Adoption in Manufacturing
Learn more about the risks and rewards of advanced manufacturing.
4. Workforce safety
Factories can be full of fast-moving machinery, hazardous materials and other perils that put worker safety at risk. Smart technology can help reduce many of these exposures:
- Sensors can warn employees of dangerous environmental conditions.4
- Robots may take over strenuous, repetitive and other tasks that are difficult or unsafe for humans to perform.5
- Wearable sensors can provide information to help inform worker decisions, teach skills, promote collaboration, prevent injuries and potentially save lives.
Benefit: Technology can help employees work smarter and safer, and it can help to minimize workplace accidents and injuries. This may help reduce costly workers compensation claims and the need to fill in scheduling gaps while injured workers are recovering.
Risk: Technology can also expose workers to new hazards, such as moving machinery and robotic parts, or equipment that performs in an unexpected way because of programming errors. To minimize these risks, it’s vital for manufacturers to anticipate and manage the dangers and adapt smart equipment with appropriate safety features.
5. Customer insights and product innovation
With new data collection and analytics capabilities, manufacturers may gain insights to help drive product innovation and better respond to customer demand:
- Products equipped with smart sensors may allow manufacturers to track purchase patterns and adjust production volume in real time to meet consumer needs.
- Wireless sensing devices can collect data on consumer product usage, which may allow companies to quickly jump on product innovation opportunities.
- Data culled from maintenance records, returns information, market research, customer feedback and other sources can inform product updates and drive new product development.6
- Using 3D and 4D printers may help manufacturers rapidly design and build products tailored to specific customer needs.
Benefit: Manufacturers can be more responsive to customers and make informed product decisions to drive competitive advantage. They can also adjust recommended maintenance schedules for equipment based on performance, which may lead to greater customer satisfaction. 3D and 4D printing may enable quick product turnarounds and on-demand production.7
Risk: Connected devices do no good if they are not up and running. Not all sensors are created equal, and they have different cybersecurity capabilities that product security teams must understand. For optimal performance, sensors that provide continuous uptime reporting must be extremely reliable. This may be vital for the manufacturer's informational needs and essential for a customer that relies on the device.
6. Sustainability
As concerns about the environment grow, many manufacturers may be prioritizing the sustainability of their operations. Smart sensors and data analytics may facilitate this process, helping manufacturers identify specific opportunities to:
- Become more efficient.
- Improve resource planning and avoid overproduction and underuse.
- Conserve energy and natural resources.
Benefit: Using smart technology to achieve sustainability goals may help manufacturers reduce material requirements and lower energy consumption and waste potentially lowering operating costs. These efforts may also help strengthen a manufacturer’s brand and reputation and build public trust.
Risk: Manufacturers may need to make a large initial investment in new processes and technologies in order to achieve their sustainability goals.
Advanced manufacturing presents many opportunities for manufacturers to increase efficiency, productivity and profitability. With these potential benefits come new risks. Understanding and addressing these risks may help manufacturers fully capitalize on the advantages of – and their investment in – smart manufacturing.
Sources
1 https://world-class-manufacturing.com/tpm/pm.html
2 https://www.atriainnovation.com/en/sensors-for-production-lines/
3 https://atos.net/en/industries/inside-smart-factory-white-paper
4 https://www.ncbi.nlm.nih.gov/pmc/articles/PMC7731246/
5 https://ecorobotics.com/industrial/6-ways-robots-can-be-used-to-address-unsafe-working-conditions/
6 https://www.sas.com/de_ch/whitepapers/imm-st-aberdeen-group-marketing-analytics-for-manufacturing-2317312.html
7 https://www.travelers.com/iw-documents/business-insurance/tech-3D-whitepaper-BTCWH.0003-D.pdf