How to Limit Supply Chain Disruptions Due to Critical Equipment
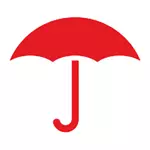
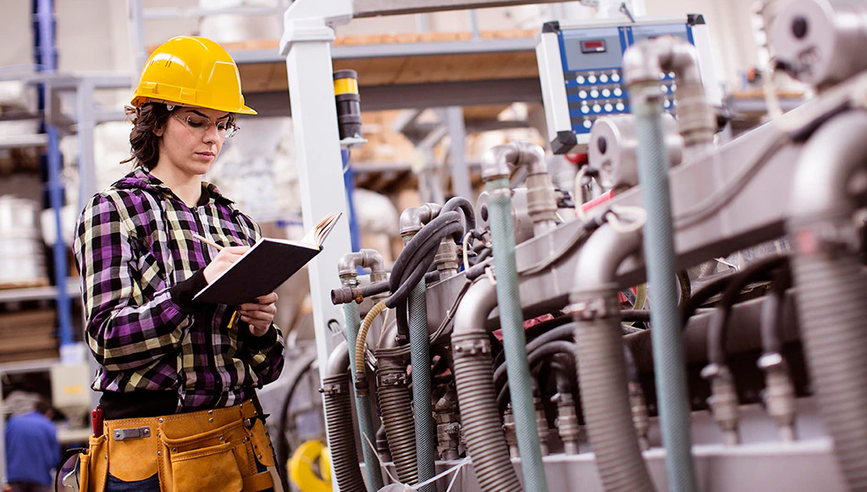
For many industries, when a piece of equipment breaks down or is destroyed, a replacement can be brought into play quickly, even if at a great expense, so production can continue.
In manufacturing, however, machinery is often highly specialized with long lead times for replacement. Purchased years before a breakdown, it may have been heavily customized over time to meet specific needs. When a critical piece of equipment cannot be repaired, a replacement may take months to replace, regardless of the cost.
Ways to manage critical equipment risks
Many manufacturers may already have a business continuity plan for what to do when disaster strikes, and production comes to a halt. However, many plans fail to address all potential bottlenecks, such as when a critical piece of equipment is damaged, destroyed or fails. The most effective plans help companies prepare for an event, protect assets, respond to emergencies, and recover fully operational capabilities in a timely manner.
Create a business continuity plan that includes key equipment
Consider the following checklist to create effective contingency plans for key equipment:
- List of key equipment. The first step is to identify key equipment, taking note of any factors that could make it difficult to replace or repair. Key equipment is critical to the operation of the business.
- Inventory of spare parts. Identify all spare parts that are critical to operations and are kept on-site. Depending on the time sensitivity, maintain a list of sources for purchasing necessary parts that could be used to repair or replace a non-functioning piece of equipment. Each year, the list should be updated with pricing and delivery times for obtaining necessary parts.
- Contractors. Identify several contractors who are qualified to work on or repair equipment, including information about their capabilities and availability.
- Rental equipment. Develop a list of sources for rental equipment, with details about cost for rental, set-up, breakdown, shipping both ways and estimated time from placement of order to start-up.
- Business loss alternatives. To avoid losing sales or falling behind on contractual obligations, consider several alternatives if equipment loss disrupts production. These include planning with other manufacturers to outsource work during an emergency, keeping inventory on hand to provide products to customers when the manufacturing line is down and running other equipment for longer hours (requiring overtime shifts) to make up for lost production.
- Connected risks. Because of their many applications, Internet of Things (IoT) devices are finding their way into every sector of manufacturing. Use of this technology can help to improve production efficiency and quality, but there are inherent risks – many of which some manufacturers are not prepared for. If your operations include connected IoT systems, learn how manufacturers minimize their exposure to IoT risks.
Identify supply chain pressure points
Protecting critical equipment can help minimize the impact of internal bottlenecks that could put your business at risk. You can address the many exposures in your supply chain by taking advantage of tools (like the Supply Chain Pressure Test that can help you evaluate your supply chain for weaknesses) and expertise that Travelers offers.