3 Key Ways to Protect Oil and Gas Operations from Pollution Risks
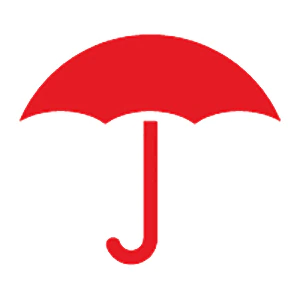
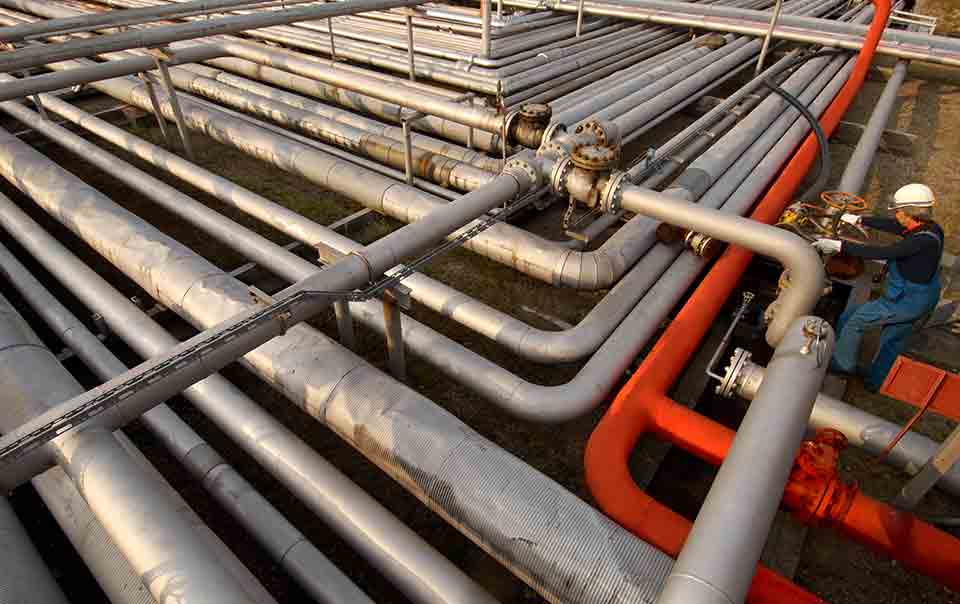
An oil spill or gas leak can often result in potential harm to the community where it occurs, as well as to the environment. Oil and gas companies that perform regular preventive maintenance of aging pipelines, tank batteries and production equipment can put themselves in a much better position to control pollution risks and to respond quickly if confronted with severe weather such as hurricanes and other natural disasters.
“Having a proactive mindset around periodic inspection and routine maintenance can help companies identify potential problems,” said Erich Watkins, a Travelers Oil and Gas Risk Control professional.
Some key ways to help control pollution risks include preventive maintenance of aging pipelines, gathering lines and flow lines, lightning protection on production equipment and proper installation procedures of polyethylene pipe (poly-pipe).
1. Preventive maintenance. Investing in maintaining infrastructure will help to reduce the likelihood of a pollution loss. Instead of responding to an incident after pollution damage has occurred, periodic inspections can allow companies to identify and repair potentially damaged production equipment before trouble strikes. Having a program to proactively check and replace aging pipe and equipment can be especially important as time passes, Watkins noted, since original installation records may be inaccurate or unavailable.
Develop a preventive maintenance plan that documents the policies and procedures to follow to help ensure that your equipment is in good working order. Have your plan account for pipelines, flow lines, gathering systems, tank batteries and other equipment specific to your operations that might present a pollution risk.
The age, type and operating conditions of pipelines and other production equipment, including pressure, flow and the type of oil, gas and/or saltwater, can affect how often the equipment needs to be inspected and replaced. Gathering lines and flow lines may be buried below the surface where visible leaks cannot be detected. In this case, it is important to consider hydrostatic pressure testing to help detect leaking and deterioration of pipes.
Having a proactive inspection and maintenance program can help to identify potential pollution sources.
Erich Watkins
Travelers Oil and Gas Risk Control Professional
2. Lightning protection. Saltwater tanks at oilfield production sites can be particularly susceptible to lightning strikes. Because of the corrosive nature of saltwater, fiberglass tanks are often used to store the product. As a result, static electricity can build up in the fiberglass tanks, making them attractive to lightning strikes that can damage the tanks and lead to spilled contaminants. Those contaminants can spread to neighboring land, crops, houses and waterways if secondary containment is not present or maintained.
When lightning strikes a tank, oxygen in the space can also act as an ignition source. As a result, this can elevate the risk for a fire or explosion. The National Fire Protection Association’s standard NFPA 780 details installation requirements to protect people and property from fire risks and other hazards related to lightning strikes.
In addition to installing lightning protection, maintaining secondary containment around the tanks can provide an important additional line of defense. If a spill is limited to inside the secondary containment, it is easier to clean up than if it expands to contaminate the soil, surface water and groundwater surrounding the area.
3. Poly-pipe installation. Poly-pipe has gained popularity in the oil and gas industry recently because of its flexibility and ease of installation. However, proper installation procedures are necessary to maintain its integrity. When poly-pipe is being installed, appropriate field oversight and documentation during the installation process need to be applied. Routine planned inspections to help ensure that installation work is being conducted properly should also be performed. A subcontractor’s ability to install and maintain these systems correctly can help guard against failures.
Often, gathering lines and substations are maintained by an operator or a contracted roustabout company. Operators that are performing these tasks themselves need to ensure their staff are qualified to do so and have the proper equipment. When lines need to be repaired, they must be isolated from the rest of the piping system, which requires a squeeze-off process using specialized equipment. Shortcuts taken by contractors using improper equipment to perform this process can lead to failure of the pipe, resulting in fire, explosion and injury to workers.
Lastly, the use of poly-pipe for saltwater disposal lines can have a higher rate of failure, leading to higher loss potential. A greater emphasis on inspection and maintenance programs for these systems is beneficial.
Preparing for major storms
Though early and complete preparation for a large storm may be impossible, proactive preventive maintenance can help to minimize potential damage. If companies receive sufficient notice of a large storm such as a hurricane, precautions can be taken at lease sites to help minimize pollution events. For instance, some companies will remove crude oil from tank batteries and refill the tanks with saltwater to help prevent them from tipping during a flooding event. Other precautions include securing the wellhead and other equipment on-site to minimize damage, as well as removing items that are considered temporary that could easily be swept away during a flood.
After a major storm, it’s important to inspect sites to check for damage and replace any impaired piping, earthen berms and secondary containment units so they will be fully functional the next time they are needed. “It’s difficult to predict the outcome of a storm, but having good programs in place to respond after an event can help to minimize pollution exposures,” Watkins said.
When preparing for a potential pollution event, it’s important to take a proactive approach. Conduct regular drills to simulate how employees will respond in an actual emergency. Contracting with an emergency response vendor in advance can not only help reduce response times, but may also allow you negotiate favorable terms for labor and equipment rates before a storm is in the forecast. These actions can help reduce costs following a significant weather event. Involve your insurance carrier early in the emergency response, cleanup and remediation process, particularly those that have experience dealing with similar situations.
Maintain a proactive risk management point of view in your approach to safeguarding your oil and gas operations. It’s a vantage point that can help protect your company in more ways than one.