3 Steps to Help Attract and Retain Skilled Manufacturing Talent
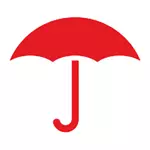
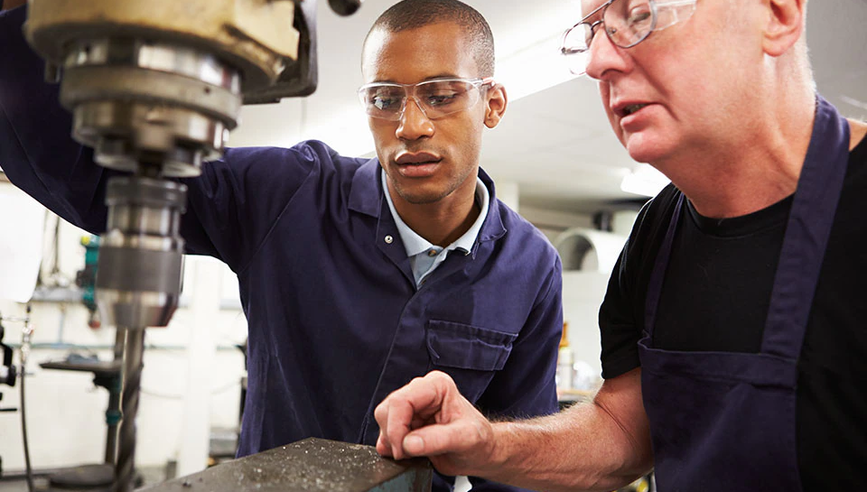
As technology plays an increasing role in advanced manufacturing processes, and as experienced workers eligible for retirement begin to leave the workforce, the manufacturing skills gap continues to grow. Manufacturing companies who can attract, develop and retain skilled workers may have a competitive advantage in a marketplace that rewards efficiency, nimbleness and rapid turnaround times.
A recruiting and onboarding strategy that clearly spells out the requirements of the job and provides support and continuous training throughout the employee’s career can position manufacturers to meet customer demands and grow their businesses while also developing their employees. Here’s a look at the manufacturing job landscape and some strategies that can help manufacturers find and keep manufacturing talent.
A growing manufacturing skills gap
Finding and training employees to operate sophisticated equipment takes an investment of time, resources and a dedicated process, so retaining them can become critical to maintaining uninterrupted production. An industry survey by the Manufacturing Institute revealed that it takes an average of 70 days to recruit skilled production workers,1 and further on-the-job training on sophisticated and often customized production line equipment may mean additional time before new hires are ready to hit the manufacturing floor.
Workplace safety is also a key reason to retain existing skilled workers, who have gained experience in the company’s safety culture. Travelers research shows that almost 28% of workplace injuries occur within the first year of employment.
One study estimates that as many as 6 out of every 10 positions may go unfilled or not be filled in a timely fashion, forcing businesses to look for alternative solutions.2 This could mean having to hire less qualified candidates to fill the position, which could create new risks. For U.S. manufacturers, it’s getting harder to fill middle-skill jobs, which require advanced training beyond a high school degree but less than a four-year college degree.3
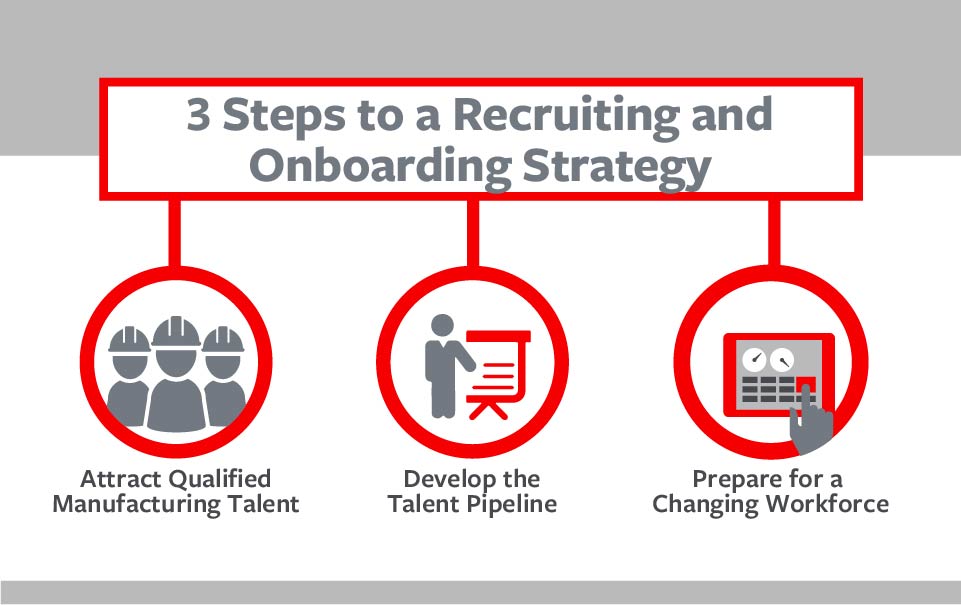
Step 1: Attract qualified manufacturing talent
Encouraging applications from candidates who are qualified to perform the required tasks will help drive retention and job satisfaction after they join the company. “As a start, manufacturers can design an authentic recruiting message that accurately describes the job demands,” says Robert T. Bell, a Travelers Risk Control Technical Director.
Designing effective onboarding programs can help engage new hires. Nearly 40% of employees leave within the first year of hire.4 Setting a realistic expectation of the job and company safety culture can help employers reduce the loss of new employees. Here are some other ways to attract qualified manufacturing talent.
- Create clear, accurate job descriptions. The job posting can include the expectations of the position, the required special equipment and the required tasks, as well as a description of the company culture and the importance of safety across the organization.
- Identify key characteristics for successful candidates. For key positions, manufacturers should identify what skills and background the ideal employee would possess and then use that information to actively recruit candidates who possess those skills, rather than waiting to review applications of candidates to discern which may be a good fit for the job.
-
Be willing to train promising candidates. When there is a shortage of qualified applicants, manufacturers may consider candidates who might not yet possess all of the technical knowledge but have the aptitude and interest to learn once they are hired. Apprenticeships and on-the-job training can help bring workers up to speed.
Step 2: Develop the talent pipeline
The pace of change in the manufacturing industry requires continuously training and developing existing employees. In addition to preparing companies to adapt new technologies and processes, internal training programs can be more efficient than recruiting workers who already possess new and more advanced skills.
- Build your middle-skills talent pipeline. Anticipate future needs for middle-skilled employees. A recent Harvard Business School report on the middle-skills gap encourages employers to think of sourcing middle-skills talent with the same rigor as they optimize their materials supply chains.5 Workforce planning can help prevent a reactive approach to filling positions.
-
Consider partnering with the community. Manufacturers are seeing the need to develop partnerships with community colleges and other local schools, with 72% describing such programs as an effective strategy to develop a skilled production workforce.6 Partnering with local schools can help manufacturers shape programs to help ensure graduates possess the specific skill sets they require.
Step 3: Prepare for a changing workforce
More than 10,000 workers per day are estimated to turn 65 between now and 2021.7 As Baby Boomers age and prepare to retire, manufacturers are facing a changing workforce and a loss of skilled talent. Manufacturing companies need to support their multigenerational workforce and help ensure that experienced workers transfer their knowledge to the next generation.
- Provide continuous and tailored safety training. Know the characteristics of your workforce and give them the resources they need to be safe and successful. Designing safety programs that take advantage of learning theories can help engage your entire workforce, from recent graduates to experienced workers.
-
Create knowledge transfer programs. The loss of a skilled employee can have a significant impact on a business. As older workers approach retirement, manufacturers can create knowledge transfer and mentoring programs to involve them in training the next generation.
Turn the skills gap into a competitive advantage
Manufacturers should plan now to avoid having a growing skills gap affect productivity and safety. Beyond the significant investment involved in hiring qualified employees, manufacturers may not be able to fill open positions in time to meet customer demands. Proactively attracting the right qualified talent and investing in ongoing training and development programs can help keep workers engaged, encourage the retention of skilled employees and prepare manufacturers to be more competitive in the marketplace.
Sources
1,2 http://www.themanufacturinginstitute.org/~/media/827DBC76533942679A15EF7067A704CD.ashx
3 https://newsroom.accenture.com/article_display.cfm?article_id=6253
4 http://www.equifax.com/business/workforce-insights/turnover
5 http://www.hbs.edu/competitiveness/Documents/bridge-the-gap.pdf
6 http://www.themanufacturinginstitute.org/~/media/827DBC76533942679A15EF7067A704CD.ashx
7 http://www.pewresearch.org/daily-number/baby-boomers-retire/