5 Steps for Product Liability Risk Management
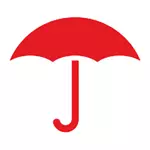
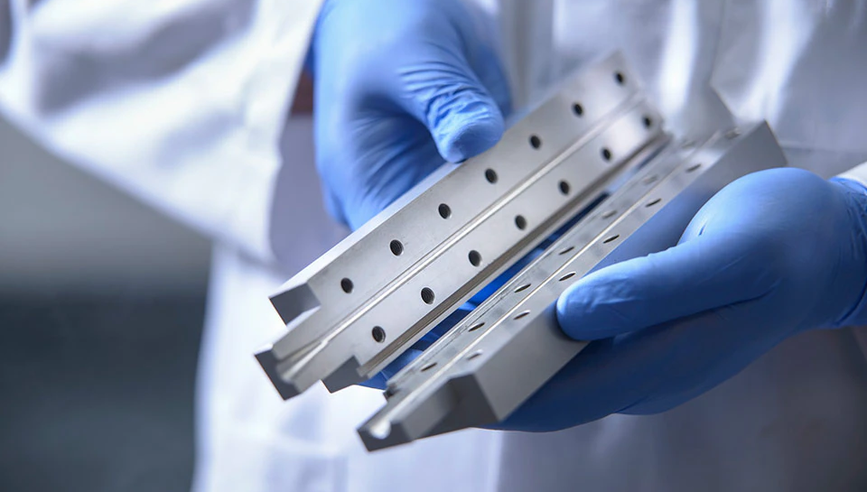
Ensuring that your product is safe from risks may seem like a daunting task. Begin to protect your company by incorporating the five steps of product liability protection. Your control of product liability may vary depending on the stage in your product’s life cycle. During development and production, you have significant opportunity to build in safeguards against potential liability claims.
Consider the next five steps as the beginning of a comprehensive product liability protection program.
1. Transfer risk through management of suppliers
A risk transfer program helps your business avoid financial vulnerability to damages and claims due to liabilities caused or contributed to by others. Without effective risk transfer, decisions of liability are often made after the fact, in court. It is much better to have such decisions documented in writing and at the beginning of a business relationship. Legal agreements can be designed to assist you in transferring risk. Work with a qualified attorney familiar with product liability law to draft these agreements at the beginning of a business relationship.
- Hold harmless agreements help ensure that your contractors and suppliers are contractually responsible for their own negligence and/or errors and omissions in the case of a claim.
- Statements of financial responsibility, e.g., certificates of insurance, can help your company avoid bearing financial responsibility for product-related claims by confirming that a contractor or supplier has the appropriate insurance in the case of a claim.
2. Managing supplies and imported goods
Companies that import products, components, raw materials and sub-assemblies subsequently provided to an end user may bear sole responsibility for certain safety requirements. They may be responsible for verifying that the imported product complies with applicable industry standards and government regulations, and confirming that proper safety warnings, labels and instructions are provided for the end user. Importers should strive to gather pertinent information from suppliers that might be needed in light of these responsibilities and in the event of a subsequent claim.
3. Build safety into design
Hazards and risks can often be eliminated or controlled in the product design phase. When designing products, a safety review should take into account how a product will be used and the kinds of hazards that may result. Products should comply with industry and government safety standards. Labels, warnings and instructions should adhere to these standards and be prominent, understandable and provided where applicable. A regularly scheduled safety review should confirm that products comply with the latest standards.
4. Keep essential records
Manufacturers should establish documentation policies to meet applicable regulatory requirements and business objectives, while also preparing for the possibility of product liability claims.
- Keep copies of customer design specifications and product orders, including customer sign-off on final designs. Establish an engineering change order system to document any change and provide a clear and complete reason for the change.
- Develop written procedures and instructions that describe the flow of the product through the manufacturing process and quality control steps. Keep documentation to help verify the quality and conformity at each of the quality control steps.
- Establish a document retention policy to help ensure preservation of documents important to the investigation and defense of product liability claims.
5. Enable and review customer feedback
Every year, defective, faulty or misused products cause serious injuries, property damage and business interruption. In extreme cases, product recalls, high-profile negative publicity and loss of goodwill may occur. Many of these incidents can be avoided if manufacturers or distributors review the complaints and feedback from their customers. Such information can help a company take positive steps at an early stage to minimize or avoid product issues and exposures. Making it easy for consumers to share their concerns can help companies respond to consumer satisfaction needs and create increased opportunities for improving products and services.
Our product liability specialists work with businesses across a broad spectrum of industries to evaluate the liability aspects of their business. The insights we gain in our everyday conversations can help you understand the liabilities you may face as you bring products and services to market.