Resuming Building Operations After an Extended Shutdown

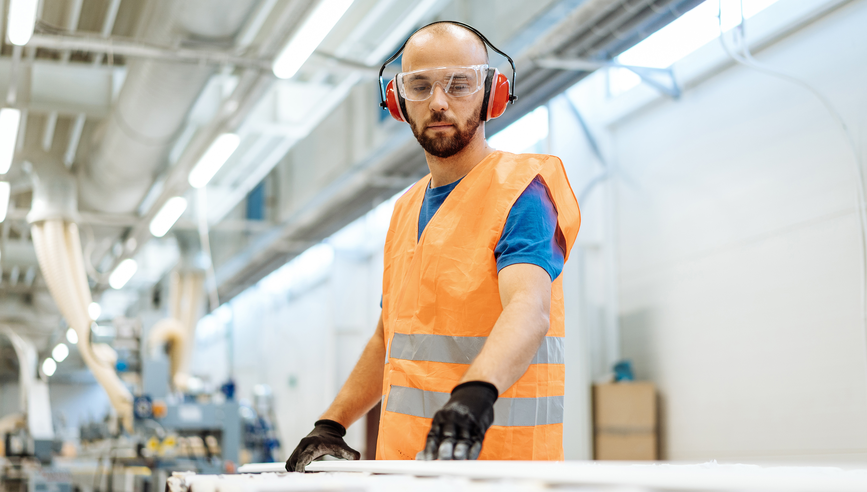
Buildings and equipment that may have been left idle or reduced in capacity due to an extended shutdown can lead to quickly deteriorating conditions and other issues that arise when a building is not routinely attended.
It is important to bring together individuals representing your primary operations in the early stages of developing your reopening plan. This can help in establishing a consistent and coordinated approach. Be sure to identify and communicate responsibilities and roles for each team member. The roles should align with individuals' areas of expertise – whether it be the building, employee safety or procedure development. Regular communication among team members can help to reduce potential oversight or duplication of efforts and help ensure a successful implementation of your plan.
Building envelope
Evaluate the building envelope – the walls and roof – to ensure it has not been compromised during the shutdown, as roof maintenance may have lapsed, and your building may have sustained damage due to severe weather. Inspect interior walls and ceilings for signs of water damage, cracks or settling of foundation walls. If safe to do so, access the roof and visually inspect roof-mounted equipment for signs of damage. Consider hiring a licensed contractor to complete the inspection if you cannot safely access the roof. Also check the roof covering and flashing for signs of damage. Be sure to clean out debris located around roof drains to help prevent standing water.
It is also important to inspect gutters to make sure they are free from debris and are discharging water away from the building. Check windows to ensure there are no broken panes or signs of water damage. If there is a sump pump in the basement of your building, verify it is functioning properly.
Electrical
In most cases, electrical systems will have remained in service at significantly reduced load during a property shutdown. Have a qualified electrician restore electrical loads slowly to prevent damage to electrical systems; have maintenance personnel assess equipment operation as power is restored.
Emergency power systems, such as emergency power generators or Uninterruptible Power Supply (UPS) systems, should be tested as soon as practical in accordance with the original equipment manufacturer’s (OEM) guidelines and normal practices. A qualified individual familiar with the operation of the equipment should physically inspect it and observe the emergency equipment testing.
If the electrical distribution system was de-energized during a shutdown, a qualified electrician should inspect all electrical panels prior to reenergizing the system. Extreme caution should be taken to prevent unexpected personal safety hazards while reenergizing the system.
HVAC and plumbing
In most cases, HVAC and plumbing systems will have remained in service during an extended shutdown. Whether or not the systems were shut down, their proper operation should be verified as soon as practical prior to re-occupancy of the buildings.
Qualified contractors or employees familiar with the proper operation of the equipment should verify that the equipment has no signs of leakage and is maintaining proper temperature, that fluid levels are as expected and, where applicable, that the equipment cycles on and off in accordance with normal operating parameters.
Efforts should be made to flush the building’s water system to help remove the potential for mold or bacteria buildup.
Emergency systems
If your property was shut down or operations were limited due an extended shutdown, check and confirm that your fire alarms and sprinkler systems are functioning properly. Begin by reviewing the records of the last inspection or service and complete the inspection, testing and maintenance that may have lapsed.
- Fire detection and alarm systems should be checked in accordance with NFPA 72, National Fire Alarm and Signaling Code. Smoke and heat detectors should be visually inspected. If you use a monitoring company, ensure that it receives supervisory and alarm signals.
- Sprinkler systems and fire pumps should be maintained in accordance with NFPA 25, Standard for the Inspection, Testing and Maintenance of Water-Based Fire Protection Systems. Travelers also has maintenance guidelines. If a sprinkler system was shut off, it should be promptly restored and tested. Begin by completing a self-inspection to identify what can be done in-house and what requires a contractor.
- Inspect all control valves to ensure that they are in the appropriate positions.
- Inspect sprinkler riser pressure gauges, record the readings and compare them to previous results.
- Run a churn test of the fire pump if your building has one.
- If it has been more than three months since the last service, a qualified contractor should conduct a 2-inch main drain flow test on each riser and test the water flow alarms.
- Ensure that life safety systems are tested and maintained in accordance with NFPA 101, Life Safety Code. Conduct a 30-second test on all egress lighting. If your facility includes additional life safety systems such as fire doors or smoke control systems, be sure to inspect, test and maintain them as necessary.