Why Now Is the Time for Manufacturers to Review Workplace Safety Programs
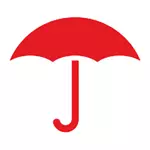
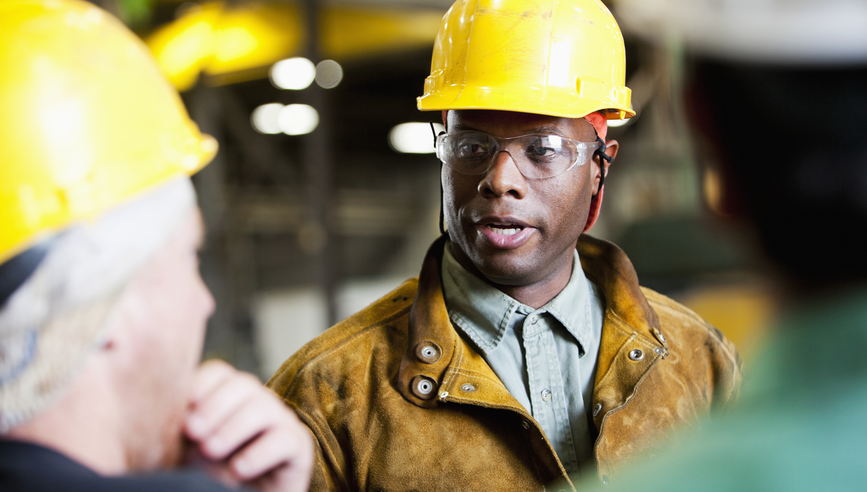
Establishing and nurturing a culture of safety remains one of today’s biggest challenges for manufacturers. Generational shifts have reshaped workforce norms and raised expectations for employer responsibility in workplace safety.1 In addition, the Occupational Safety and Health Act of 1970 (OSHA) has increased the number of workplace inspections across the nation.2
An unwavering culture of safety can help safeguard employees and improve interactions with OSHA. It’s always a good time for your organization to review safety regulations and your workplace safety programs and policies. Ensuring that safety programs and policies are well-documented, comprehensive, up-to-date and comply with relevant regulations and laws is fundamental to helping mitigate workplace risks and meeting OSHA standards.
Five ways to modernize your safety program.
“Safety management works well when the focus is on creating a culture that your employees and your management can feel good about following,” said Chris Hayes, Assistant Vice President of Auto and Workers Compensation Risk Control at Travelers. “Often that starts with effective hiring, training, employee engagement and communication. And then, if accidents do happen, how do you respond? How do you provide quality care and bring people back to work in a way that further earns the trust of all employees?”
By addressing unsafe conditions before they lead to injuries and having a solid response plan in case injuries occur, companies can help build a strong culture of safety. Adding in a process of continuous review with the following steps can help keep programs current.
1. Bring the new generation into the workplace safety conversation.
As new generations enter the labor pool, they may be more vocal than prior generations in calling for meticulousness from employers or reaching out to external governing agencies if they have concerns.
These digital natives can help companies develop applications, user-friendly forms and other means to alert management and safety committees of potential safety issues early, before a major incident occurs. Employee engagement in the process can be critical. Communicating effectively, openly and honestly with workers who are on the job day in and day out can help deepen a company’s understanding of potential risks and the safety practices to avoid them.
“Generation Z, the 69 million young Americans born between 1997 and 2012, were shaped by climate change, COVID, the 2008 recession and social justice movements. Gen Z (and millennials before them) have grown up in a world that has been unstable and unpredictable, making them highly risk averse and cautious. Companies cannot simply rely on their stature or history to win the trust of Gen Z but must instead proactively earn it,” says Jacqui Heidelberger, Assistant Vice President of Market Research at Travelers.
2. Keep current on OSHA regulations and inspections.
OSHA was passed to “assure safe and healthful working conditions for working men and women; by authorizing enforcement of the standards developed under the Act; by assisting and encouraging the States in their efforts to assure safe and healthful working conditions; by providing for research, information, education, and training in the field of occupational safety and health.”3
Understanding OSHA is a smart place to start when developing an effective safety management plan.
Consider these questions when developing a workplace safety management plan:
- Have you appointed someone in senior management to be accountable for administering organization-wide OSHA program compliance?
- Does your company have a procedure for hazard identification and assessment, including maintaining accurate and up-to-date records of workplace hazards, accidents and near misses?
- Does your company evaluate and verify the effectiveness of your workplace safety and health controls and related training programs?
- Are programs documented and designed by knowledgeable staff who understand the most recent standards? Are they implemented successfully in the daily work environment?
- Does your business have a robust process to continually evaluate worksite operations to determine health, mechanical and ergonomic hazards as well as methods to help eliminate or control them?4
MyTravelers® online risk control tools and resources offer customers a full collection of resources geared to aid in understanding and following OSHA standards, including:
- Industrial Hygiene Hazard Assessment Models
- Communications Checklists
- Revised Respiratory Protection Standards
- Exposure Limit Resources
Creating a safe and healthy work environment may also benefit employee mental health, which is particularly important as today’s workers increasingly prioritize psychological well-being.5 Implementing wellness programs and offering mental health support can play a significant role in facilitating timely recovery after an injury. According to Travelers workers compensation claim data, more than 40% of employees who missed workdays due to injury have experienced a psychosocial barrier to recovery.6 “Factors unrelated to an individual’s injury, such as fear, unrealistic expectations, lack of sleep or minimal social support, can hinder the recovery process,” said Dr. Marcos Iglesias, Chief Medical Director at Travelers.
Advance workplace safety with services to help injured employees recover
Key services can help injured employees feel supported and move forward in their healing so they can return to work at the medically appropriate time. Travelers’ workers compensation program provides services designed to support injured employees across multiple dimensions throughout their recovery.
- Wysa for Return-to-Work, an app designed to promote the mental well-being of injured employees and facilitate a more holistic recovery.
- The Virtual Visit tool, which enables nurses and Claim professionals to conduct real-time video chats with employers, medical providers and injured employees to discuss matters pertaining to the recovery process.
- MyTravelers® for Injured Employees, a secure, web-based tool that helps individuals navigate the workers compensation claim process.
- The Early Severity Predictor® model, which helps identify which injured employees are most at risk for chronic pain.
- The ConciergeCLAIM® Nurse program, which helps injured employees navigate the workers compensation process through a one-on-one connection with a nurse.
3. Harness data to uncover risk and injury patterns and safety solutions.
Claim data can yield valuable information to drive continuous improvement plans, as can data from other sources, including your health and safety, finance and human resources teams.7 Robust analysis of past incidents, including near misses, may uncover root causes previously unnoticed. A trusted insurance carrier can help risk managers use data and analytics to identify problems and opportunities, benchmark against industry standards and share best practices for safety management.
“If employees are properly trained, included in the safety process and properly guided through an injury report and claim, they and their fellow workers are more likely to feel comfortable with the claim process as a whole,” Hayes said. “Employees should not be afraid to reach out to managers at the beginning of an injury but instead should see their incident and injury properly addressed and cared for. This emphasizes the reason a comprehensive recovery plan is essential to a successful workers compensation claim.”
Travelers’ insurance strategies for risk management can help with coaching, onboarding, accident analysis, leadership, safety and communication strategies.
- e-CARMA®, Travelers’ risk management dashboard, is a customizable analysis tool that gives business customers access to data that can help identify accident trends, analyze root causes of loss and learn what factors impact safety in their organization.
- With one of the largest Risk Control departments in the country, Travelers regularly deploys risk control professionals with specialized skill sets to assist manufacturing customers in managing specific exposures. These can include injury management, fire protection, product liability, ergonomics, equipment breakdown and more.
4. Train employees on safety standards early and often.
It is increasingly important to thoughtfully onboard employees and contractors as they enter your workplace. According to Travelers data, more than one-third of workplace injuries occur within the first year of employment, and these new-hire injuries account for almost one-third of claim costs.
Even experienced employees can be at higher risk for an injury if they are new to the role or department.8 It may be beneficial to identify new positions and perform job safety analyses, breaking down each step, identifying associated hazards and defining a safe work method.9 When planning safety training, be sure all company communications are clear and in the appropriate language for non-native English speakers.
5. Learn from safety programs data and injury reports to continually improve.
Employees are more likely to support a safety initiative if they see visible evidence of earnest support from leaders. Upon communicating effectively using a variety of formats (meetings, emails, posters, etc.), reinforce your commitment to compliance with training and safety tools and support across all areas, including workers compensation claims. Address reported complaints, injuries and near misses efficiently and completely and circle back to put prevention strategies in place. Comprehensive transitional duty and injury management are essential and give businesses a competitive advantage, helping them reduce risk, claims filed and dollars spent away from business and innovation.
Manage safety risk with attention to employees and processes.
As the manufacturing industry evolves, so should safety programs. Between new OSHA requirements, advances in technology and machinery, and generational changes in the workforce, there will be many opportunities to review safety management plans and improve processes and procedures to meet new conditions.
Manufacturers can take advantage of the knowledge and resources available through their insurance carriers to help inform a modern approach to fortifying a workplace culture of safety. When data, analytics and a holistic strategy come together, companies may be better equipped to meet workers’ safety expectations and maintain regulatory compliance.
Learn more about workers compensation policies and insurance for manufacturers.
Sources:
1https://www.ncbi.nlm.nih.gov/pmc/articles/PMC7737298/
2https://www.osha.gov/news/newsreleases/trade/12032019
3,4https://www.osha.gov/sites/default/files/publications/osha3021.pdf
5https://www.hhs.gov/sites/default/files/workplace-mental-health-well-being.pdf
6https://www.travelers.com/resources/business-topics/employee-wellness/generational-impact-workplace-mental-health#biopsychosocial
7https://www.travelers.com/resources/business-topics/workplace-safety/tips-for-data-driven-risk-management
8,9https://www.travelers.com/resources/business-topics/workplace-safety/managing-the-risks-of-injury-to-first-year-employees
10All data included is Travelers indemnity claim data, in 2016-2020 accident years. Zero-dollar claims excluded. Valued 12/31/2021. Losses are unlimited and undeveloped. Unless otherwise noted, data points highlighted represent claims across all employees in the manufacturing industry.