How Technology Is Transforming Construction Job Site Safety
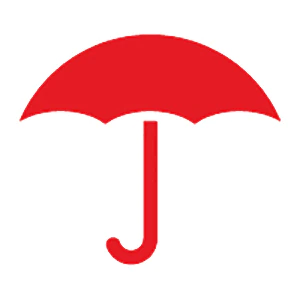
Chapter #1 Chapter #2 Chapter #3 Chapter #4 Chapter #5 Chapter #6 Chapter #7 Full Webinar Video
Innovative technology continues to play an important role in improving job site safety, and now it can help manage your construction firm’s response to the pandemic. Technology can help essential workers remain safe by maintaining social distancing, and if an employee tests positive for COVID-19, contact tracing can be performed.
Chapter #1
How Construction Companies Are Using Technology on the Job Site
This is a time of digital transformation at construction sites, according to Bob Dolan, Vice President of Sales at Triax Technologies. Smarter, connected job sites that provide real-time data on worker locations can increase efficiency and reduce response time to injured employees. This greater visibility has proven especially critical during the COVID-19 pandemic, allowing companies to respond rapidly in the event of a positive case of COVID-19 at a job site.
(DESCRIPTION)
Bob Dolan speaking over slide 3 and video in top right corner. 3 various images displayed. Text, Smarter, more connected jobsites. Logo, Travelers.
(SPEECH)
BOB DOLAN: You know what we're seeing in the construction market with contractors is the technology of every type, in every shape, size is really being infused into the construction projects at what I'm referring to as a time of digital transformation on construction sites.
And the difference between what we were three years ago, and where we are today is night and day. These technologies, obviously ours is a real time platform, but these are tools that help in terms of safety, in terms of education, utilized in VR, sensors, you name it.
We're seeing quality being driven through technology and visibility to the data to those project teams so they can act appropriately and efficiently and basically in real time.
Our solution obviously is a unique one in that it does offer real time solutions where users have the ability to get immediate notifications directly from workers around safety issues be at an injury or near miss because we can identify where workers are generally speaking and zones – floor to floor. We also reduce response time to injury.
So those types of infusions of technology that really reduce response time drive efficiency around work, around safety, around things like evacuations. We're seeing contractors. Look at those for the value, they drive and the immediate ability to access information and take action.
So that can be again on safety issues, it can be built around certifications, OSHA compliance.
In short what we see and what we do strive to do is not only collect the data, but most importantly, drive it towards the safety professional or project leader that makes it accessible in real-time.
So giving that greater visibility to what's going on we positively feel and have seen positive impact on safety and construction and industrial sites.
(DESCRIPTON)
Travelers Logo
Chapter #2
Changes in the Construction Industry Since COVID-19
Proximity tracing sensors help manage COVID-19 social distancing measures at job sites, with sensors that send an alert if employees are within 6 feet, reminding them to maintain a greater distance. “It’s allowed our staff who were managing the job site to feel comfortable that they were addressing a new safety exposure that really just dropped in our lap,” explains Don Naber, Senior Vice President, Director of Risk Management at Gilbane. The sensors also aid contact tracing efforts by determining which workers were in the same area as an individual with COVID-19 exposure.
(DESCRIPTION)
Don Naber speaking over slide with his video displayed in top right corner. Image of construction workers. Text, Keeping workers safe during COVID-19 with alert systems. Logo, Travelers.
(SPEECH)
DON NABER: Um, it's, it's obviously much like everything else in our lives. A significant amount of change. You know, with all the various states and the mandates that they were imposing relative to social distancing wearing masks and then on top of that you've got, you know, what do you need to do from a construction standpoint, you know, each and every day and recognizing that people need to be interact with one another and sometimes be close.
We work very closely with Triax on their spot R system to see if we could find a way to develop something a little bit different and tracks came up with Proximity Trace. And what it allows us to do is provide clip sensors for each of our each of the employees on site. As individuals get within six feet of one another, then the eclipse will send off an alert identifying that they're close to someone.
So it's helping them understand that when you do get too close, maybe it's time for us to get a little bit further away from one another. But I think what was more important about and what we really worked hard on is to try and determine and understand who is in and around one another during the course of the day. So that way, in the event that somebody did contract COVID 19, test positive, etc. on one of our job sites, we had the ability to do the contact tracing without having actually having any conversations with anybody.
We could go back into the system. We would know how many people were in the in the location of this one person who had tested positive. And then in addition to that, not only understanding of those people, but where they were where this person was in the building. And where the people were that were that might have been exposed in the building as well.
So that way, it allowed us, not just to focus on a specific subcontractor or crew. But now we could expand it a little bit further and understand who may have been exposed.
It would also help us understand from a cleaning perspective at the job site, what did we need to do to clean the job to make sure there was disinfected so that way people would feel comfortable in coming back to work once we were able to open the job.
It really allowed us to communicate a lot better with the subcontractors.
It allowed us to make the subcontractors feel comfortable and just as important. It allowed our staff who are managing the jobs to really feel comfortable that they could address a new safety exposure that has really been dropped in our lap without really a whole lot of training.
And obviously for construction managers and subcontractors, safety is such a critical component and the tools that we've been able to implement around COVID-19 have really helped us better identify and manage the safety exposure that comes with this new risk.
(DESCRIPTON)
Travelers Logo
Chapter #3
Using Real-Time Data in Construction
Knowing, in real time, where workers are at the job site can help construction companies act quickly if a worker is injured. “It has allowed for rapid response in critical situations,” says Bob Dolan, Vice President of Sales at Triax Technologies. The safety technology includes a fall detection system and functionality that allows employees to report injuries and other issues with the push of a button. This data can also help companies make sure that employees are in the right locations on the job site.
(DESCRIPTION)
Don Naber speaking over slide with his video displayed in top right corner. Visualization is displayed of construction site. Text, Know where your workers are and who they’ve bene in contact with. Logo, Travelers.
(SPEECH)
DON NABER: What we're focusing on is first and foremost from an efficiency standpoint, making sure everybody's in the right spot on the construction site. This particular service is not a GPS system that is going to follow you wherever you go. It's triggered once you walk on the site with the clip that's there.
And all we care about at Gilbane is making sure that everyone is safe. What happens when people leave the job, obviously, that's not of interest to us and we obviously want to make sure that that's very, very clear. But you know when it comes to the information that's readily available to us. The one thing that we were drawn to this product is the fall detection system that's available.
And I'll allow Bob to go into that the whole system and how it works. But for us, what it does for us, it allows us to give immediate attention to people if and when they're injured on the job site. And there's a whole lot more to the system that I think Bob can do a better job going over.
(Description)
Bob Dolan speaking over slide with his video displayed in top right corner. Visualization is displayed of construction site. Text, Know where your workers are and who they’ve bene in contact with. Logo, Travelers.
(SPEECH)
BOB DOLAN: For sure, Don, I appreciate it. And I appreciate the kind words about what we do, obviously. Our focus has been since the inception of the company is to drive safety and enhanced safety on every environment we step on to through the use of the technology. So the Spotter system again is a real time 900 megahertz network. So we don't use GPS, we don't need WiFi, we simply utilize a seamless and easy to deploy network that utilizes a cellular up link to get data to people in real-time.
Our devices themselves allow for identification of freefall. They allow for a push button alerts so workers can in fact report enormous they couldn't report an injury, they can report a variety of different issues related to reducing risk. So we feel like the when it comes to safety, the real-time aspect of what we do is so critical because it allows our clients like Gilbane and others to act very appropriately and very quickly based upon a general area of reporting.
We don't say you are in this specific room, we simply say you're on this floor, kind of in this zone area. So it has allowed for rapid response in critical situations and it continues to evolve through input from customers like Gilbane that have allowed us to kind of expand the product and evolve on it within the construction environment.
(DESCRIPTON)
Travelers Logo
Chapter #4
Real-Life Examples of Technology’s Impact on a Construction Site
Technology is helping construction companies detect fraud and respond faster with medical help in an emergency. Identifying individuals who were in the area at the time of an incident allows for more expedient investigations that can help determine and eliminate potential fraud. In the case of a severe leg injury at a Gilbane site, the notification button allowed workers to quickly summon a medical professional to the scene who readjusted a tourniquet applied on scene, which likely saved the life of the injured employee.
(DESCRIPTION)
Don Naber speaking over slide with his video displayed in top right corner. Map is displayed with a key and text. A table is displayed on Historical Behavioral Reporting. Text, Wearables can help identify unsafe behaviors. Logo, Travelers.
(SPEECH)
DON NABER: A benefit here to is it from a fraud detection standpoint.
Because not only do you understand what, where, and when something occurred from a fall perspective. You also have an understanding of who are the individuals who are around at the time that that incident occurred.
So we have the ability to ask questions and investigate in a much more expedient manner than what we might be able to do without the technology because identifying all the people that may have been there without this technology is not always the easiest thing to do.
But this allows us to, like I said, identify whether it was coworkers or whether it was another subcontractor who may have been in the area.
This helps us really kind of understand things and determine if a particular accident was something that was staged or if it was something that actually occurred.
So obviously, the most important thing like you talked about Casey is getting that that quick response to give people the attention that they need, but it's also a tool to help reduce and maybe even eliminate fraud, if it were to happen at the construction site.
The other thing that you know I wanted to mention in terms of the response time is in some of the examples that we have, one of the projects that we have in Florida, we had an individual who had a very severe, severe cut on their thigh and on the on. Not only do you have fault protection or fall detection in the system, but it also has notification. So a number of people on the site were able to use their notification button to be able to notify our team on their particular project.
We had an EMT, the EMT was able to get out in a very, very short period of time and the people who were immediate to the this the incident that occurred, they applied a tourniquet. And when the EMT got there, while the tourniquet was helpful.
It could have actually if it wasn't changed or adjusted it may have caused maybe some further challenges as well. But this is somebody who actually wound up getting a number of stitches wound up back on the site the next day. So we didn't even have a last time with the situation, but the EMT said and the doctor said that had he not been or had had he not gotten the attention of, you know, with the tourniquet and so forth. There was a good chance that he would have bled out.
Value add, and when you think of something like that, it's not about the money.
It's about that somebody's life was saved in. And while there were great people around, the Triax system, brought the right people around at the right time to help solve the problem.
(DESCRIPTON)
Travelers Logo
Chapter #5
Technology Helps Identify Long-Term Risks
Don Naber describes how a wearable device’s fall detection system spotted a hidden danger that staff initially thought was a false alarm. At a popular shortcut through a job site, employees were jumping from a height of 3 to 4 feet to gain faster access to another area of the site. Eliminating the shortcut helped avoid potential soft tissue injuries over time. “At the same time, we were also fixing and enhancing the overall efficiency of the job by creating better access points for the workers,” Naber says.
(DESCRIPTION)
Don Naber speaking over slide with his video displayed in top right corner. Image of construction worker jumping off construction truck is displayed. Text, Devices reveal hidden dangers. Logo, Travelers.
(SPEECH)
DON NABER: So this is a great picture and one Bob Dolan and I lived at one of our projects where the sensors have adjustments to them in terms of detecting how far somebody may fall. Whether it's a foot, whether it's four feet, or whatever and you can adjust the sensor accordingly in the system.
And we had it set at a very low level and what it was doing it was sending off a lot of false alerts or what we believed were false alerts.
And our project team was getting very frustrated by that. So we had Bob and some others from tracks go in and just monitor for the course of the day to see if they can understand what was going on.
And what we came to the conclusion of was is that, like this picture many of the workers were jumping off the back of pickup trucks supply trucks, they were jumping from one level to another of roughly three or four feet, and that's what was causing the notifications in the system.
What when sitting down with the subs and talking to them about, hey look, you know, this is a repetitive motion problem. This is, you know, somebody who's young in the construction industry who has plans to be in it for the rest of their life.
This is something that is going to cause problems over time to your knees, your hips, your ankles, etc. But what came from it really was a bigger view than that which that's an important view.
But one of the reasons that they were doing it is because they felt that the way that the project and the site was laid out didn't give them all the access points that they needed.
So they were taking shortcuts and those shortcuts required jumping in certain areas and cutting corners.
So it helped the communication with the project team to reduce overall exposures at the site so not only were we getting rid of the immediate claim or incident circumstance, but we're also taking the taking care of the, you know, some of the long term wear and tear that could occur.
But at the same time, we're also in fixing and enhancing the overall efficiency of the job by creating better access points for the workers.
(DESCRIPTON)
Travelers Logo
Chapter #6
Employee Privacy Considerations
“Workers could be apprehensive about potential negative consequences if their behavior is tracked,” says Casey Banks, Senior Regional Risk Control Consultant at Travelers. Construction companies can communicate with employees on what data will be collected and how the data will be used, such as showing sample outputs before a wearable project begins, to ensure that it is being used for its intended safety goals.
(DESCRIPTION)
Casey Banks speaking over slide with his video displayed in top right corner. Text, Data and Security Considerations. Logo, Travelers. Two images are shown regarding Transparency and Cyber Security. Text following images.
(SPEECH)
CASEY BANKS: Employee privacy, I mean, that's always a consideration, should always be a consideration.
Anytime we're selecting a specific vendor or product, one aspect is really understanding what the data captures and what it does not capture.
And the issue here is that, and Don talked about it a little bit workers, could be apprehensive about potential negative consequences related to that data that's collected about their activities, especially wearables that track job site movement, locations.
So from that aspect, transparency matters.
It's always helpful to show sample outputs before that wearable project begins and then throughout the project as you go along, provide that information to those workers.
So just to help confirm that the data is being used for its intended safety goals and we're not trying to track that work or when they leave the job site so.
Another concern is how privacy is preserved (preserved) through the vendors use and management of that data that you're providing them.
So it is common with a lot of these vendors that personally identifiable information such as name, gender, age is used in conjunction with other data points to try to identify and look at insights into trends.
At some of the things you want to find out from the vendors and some of the things you want to ask is how they protect the data while it's in their use and whether they keep it whether they share that resulting data to third parties, which in some cases they might actually do that.
So that's always a question you want to find out. Encryption practices, removing that personally identifiable information, I think that's pretty normal process among a lot of the vendors out there, but we really can't assume that the proper levels of data security, privacy measures are in place.
So find out that information and that should overall that should be part of that vetting process with any perspective vendor that that the companies looking to hire to use the technology. So, always ask those questions.
(DESCRIPTON)
Travelers Logo
Chapter #7
Technology on the Job Site: The Future Is Now
At today’s job site, integrated technology addresses both security and COVID-19 safety concerns, scanning workers to detect temperatures and verifying mask-wearing compliance, as well as recording when the worker enters and leaves the job site through turnstile-activation systems. “Technology has done a wonderful thing in terms of helping improve access points and maintain control of who does and who does not go onto the job,” says Don Naber, Senior Vice President, Director of Risk Management at Gilbane.
(DESCRIPTION)
Don Naber speaking over slide with his video displayed in top right corner. Three images are displayed of construction workers in the field. Text per image: Past, Present, Future. Slide title: Construction Sites Over Time. Logo, Travelers.
(SPEECH)
DON NABER: And for us, the future is now that is a picture from one of our job sites that was provided the other day.
And it's integrating a number of different technologies together to establish an access point but also address some of the concerns that we're having from a COVID standpoint.
So this gentleman who is in the picture on the left side of the picture you can see that he has a mask on.
And what the white box that he's looking at is actually a temperature detecting system that was is taking his temperature, but it's also verifying that he has a mask on, which is one of the requirements of the job that he's on. This happens to be in the state of New York.
And once that's verified that his temperature is acceptable and obviously verifies the mask, he has his Triax Spot R clip on and what happens is that now that the turnstile that you can kind of see there it notifies the turnstile that that the person who is, who just had had done the temperature screen, is going to be coming through.
So he has to take his clip it, last it activates the turnstile for about 10 seconds and then the clip will open up the turnstile. So we've done a number of things here in terms of the access point we've taken care of the temperature, we verified the mask, now we've identified, who's going on to the site and we've kept the site protected from people walking on or leaving the site because when you leave you I'll show you actually have to clip out to.
So now we know who's left the site as well.
So technology has done a wonderful thing in terms of helping improve access points and control of who does and who does not go on to the job.
(DESCRIPTON)
Travelers Logo
How Technology Is Transforming Construction Job Site Safety [Full Webinar Replay]
(DESCRIPTION)
Louisa Desson speaking over title slide. Logo, Travelers. Text, How Technology is Transforming Construction Jobsite Safety.
(SPEECH)
LOUISA DESSON: Well, good afternoon. And thank you again for joining us for How Technology is Transforming Construction Jobsite Safety. I'm Louisa Desson, I'm Director and Senior Editor for Commercial Lines content here at Travelers where I write about workplace safety for our customers to help them protect and grow their business. And I know that there's no more important topic for us than workplace safety and helping our customers and their employees return home safely every day. So I'll be your moderator today and I want to thank you all for joining us to talk about this important topic.
I'll introduce our panelists.
(DESCRIPTION)
Louisa Desson speaking over slide Logo, Travelers. Text, Our Panel. Images of panelists with a brief description of each is displayed.
Text,
Our Panel
Panelist Casey Banks, Senior Regional Risk Control Consultant at Travelers
Panelist Bob Dolan, Vice President of Sales at Triax Technologies
Panelist Don Naber, Senior Vice President Director of Risk Management at Gilbane
Moderator, Louisa Desson Director & Senior Editor, Enterprise Integrated Marketing at Travelers
(SPEECH)
LOUISA DESSON: So Casey, let's start with you.
(SPEECH)
CASEY BANKS: Great. Good afternoon, everyone. I'm Casey Banks, a Senior Regional Risk Control consultant in Travelers Construction Energy and Marine Department, and I am based out of our Braintree, Massachusetts office. I've worked in the risk management field for a little over 15 years now, and currently lead several of Travelers technology and innovation initiatives with our construction customers.
(SPEECH)
LOUISA DESSON: Great, thank you. Bob.
(SPEECH)
BOB DOLAN: Good afternoon, Louisa and everybody. My name is Bob Dolan, I've been at Triax technologies in a business development capacity, since we were founded six and a half years ago.
Triax is located in Norwalk, Connecticut. And we have approximately forty employees. Our sensors and platforms have designed for rugged environments such as construction in and heavy industrial environments. The sensors drive actionable data to safety professionals project leaders that enhance safety and reduce risk. Presently, I serve as the Vice President of Sales where I work with our business development team across the United States.
And I've had the pleasure and privilege to work with Gilbane and Don Naber for the past three years, as they have deployed our products on a number of their job sites. So really pleased to be with you all today.
(SPEECH)
LOUISA DESSON: Great, thank you. And Don.
(SPEECH)
DON NABER: Good afternoon. I'm Don Naber. I'm Senior Vice President Director of Risk Management at Gilbane.
I work out of our Providence, Rhode Island office. However, I get the pleasure of traveling around the country to many of our offices and projects. And fundamentally I've been in the insurance industry for roughly 30 years and focusing on the construction side and have been in my role at Gilbane and risk management for 15 years.
And overall at Gilbane my role is to oversee all of our insurance products, but more importantly integrate the policy and procedure of what's important in managing those products and protecting Gilbane into everything that we do from a legal standpoint, operation standpoint, work very closely with safety. So overall, very interactive with most of what happens within Gilbane and happy to be part of today.
(SPEECH)
LOUISA DESSON: Great well, thank you all for joining us. We’ll start with our first question, how are construction companies using technology on the job site? Casey?
(SPEECH)
CASEY BANS: Yeah, that's a good question, Louisa.
(DESCRIPTION)
Casey Banks speaking over slide 3. Text, Text, Smarter, more connected jobsites.
Text, AI. Image, person tapping phone on device.
Text, Wearables. Image, illustrated construction worker wearing a motion sensored wearable
Text, Augmented Reality. Image, Person wearing augmented reality goggles as construction worker points
(SPEECH)
CASEY BANKS: So, from our standpoint, we're seeing everything from water sensors that are using artificial intelligence to help detect and stop leaks to contractors using exoskeletons for workers to help prevent fatigue over exertion issues.
Now, over the past six months we've started to see a lot more tech companies capitalize on the need for job sites to enforce social distancing and monitor contact tracing with worker groups.
But I think, despite the increased use of construction technology, there's still a good number of contractors out there who are really trying to figure out the best approach to leveraging things like wearables and IoT sensors and AI platforms to help them not only improve safety on the job sites, but also try and stay competitive in a world where projects are becoming smarter and more connected across the entire industry.
Now anytime we have the conversation around the use of advanced technology, we always start by asking the contractor what problem are you trying to solve? So really, what's your goal and strategy to implementing this?
Construction companies who are doing this best are asking what problems they can solve, but then they're going on to identifying deploy technology to provide solutions to those problems.
Now individual companies have their own set of exposures and risks that they're trying to manage.
So if we look at a broader set of issues faced by contractors today, we see that one of the major concerns continues to be around the lack of skilled labor and the ability to adequately staff job sites with qualified workers. So, in recent years, I know a lot of folks have turned to different methods of construction. So we've seen a lot more modular construction, we've seen more pre-fabrication to try to improve efficiency.
However, today, if we look at the job site, we're seeing things like 3D printing and even robotics being used on job sites to try and make up for that lack of available labor.
Now another concern we have on the insurance side is that a lot of our lost data tells us a significant number of injuries are occurring to employees with less than one year employment with their companies.
So if we look at that, this really speaks to the importance of onboarding, training and then ultimately the overall safety engagement of these workers. So that's where companies, we see them leveraging things like augmented reality, virtual reality devices for safety related training, using proximity detection systems to keep workers out of harm's way, from vehicles, from other pieces of equipment.
And then wearable devices to try and provide feedback to workers and also the employers on any observable behaviors. Now speaking of wearables, Bob, maybe you can give us a quick overview of what Triax is seen out there with contractors
(SPEECH)
BOB DOLAN: Sure, Casey. Thank you. You know what we're seeing in the construction market with contractors is that technology of every type, in every shape, size is really being infused into the construction projects at what I'm referring to as a time of digital transformation on construction sites.
And the difference between where we were three years ago, and where we are today is night and day. These technologies, obviously, ours is a real time platform, but these are tools that help in terms of safety, in terms of education, utilized in VR, Country sensors, you name it.
We're seeing quality being driven through technology and visibility to the data to those project teams so they can act appropriately and efficiently and basically in real time.
Our solution obviously is a unique one in that it does offer real time solutions where users have the ability to get immediate notifications directly from workers around safety issues be at an injury or near miss because we can identify where workers are generally speaking and zones floor to floor. We also reduce response time to injury.
So those types of infusions of technology that really reduce response time drive efficiency around work, around safety, around things like evacuations. We're seeing contractors look at those for the value, they drive and the immediate ability to access information and take action. So that can be again on safety issues, it can be built around certifications OSHA compliance.
In short what we see and what we do strive to do is not only collect the data, but most importantly, drive it towards the safety professional or project leader that makes it accessible in real time.
So giving that greater visibility to what's going on we positively feel and have seen positive impact on safety and construction and industrial sites. And never has that been more evident in terms of the value of data construction really in every workspace is with the arrival of a pandemic, like COVID-19.
I think this particular pandemic has seen and driven value of the unseen into far sharper focus for a lot of different environments. Why? Because the ability to determine interactions that you don't see and who's in close contact with whom has become a critically measurable event in every business environment. So our product that we introduced in May, which does exactly that has given these project teams and all work environments that ability for rapid response COVID tests come back positive or case be identified, so they can take action.
(SPEECH)
LOUISA DESSON: That's an interesting point that you bring up about this new world that we're living in. Don, what change in the construction industry have you seen since COVID-19?
(DESCRIPTION)
Don Naber speaking over slide with his video displayed in top right corner. Image of construction workers. Text, Keeping workers safe during COVID-19 with alert systems. Logo, Travelers.
(SPEECH)
DON NABER: It’s obviously much like everything else in our lives. A significant amount of change. You know, with all the various states and the mandates that they were imposing relative to social distancing wearing masks and then on top of that, what do you need to do from a construction standpoint each and every day and recognizing that people need to be interact with one another and sometimes be close.
We work very closely with Triax7 on their spot R system to see if we could find a way to develop something a little bit different and Triax came up with proximity trace. And what it allows us to do is provide clip sensors for each of the employees on site. As individuals get within six feet of one another, then the eclipse will send off an alert identifying that they're close to someone.
So it's helping them understand that when you do get too close, maybe it's time for us to get a little bit further away from one another. But I think what was more important about and what we really worked hard on is to try and determine and understand who is in and around one another during the course of the day. So that way, in the event that somebody did contract COVID 19, test positive, etc. on one of our job sites, we had the ability to do the contract tracing without actually having any conversations with anybody. We could go back into the system. We would know how many people were in the location of this one person who had tested positive. And then in addition to that, not only understanding of those people, but where this person was in the building, and where the people were that might have been exposed in the building as well.
So that way, it allowed us, not just to focus on a specific subcontractor or crew. But now we could expand it a little bit further and understand who may have been exposed.
It would also help us understand from a cleaning perspective at the job site, what did we need to do to clean the job to make sure it was disinfected so that way people would feel comfortable in coming back to work once we were able to open the job.
It really allowed us to communicate a lot better with the subcontractors.
It allowed us to make the subcontractors feel comfortable and just as important, it allowed our staff who are managing the jobs to really feel comfortable that they could address a new safety exposure that has really been dropped in our lap without really a whole lot of training.
And obviously for construction managers and subcontractors, safety is such a critical component and the tools that we've been able to implement around COVID-19 have really helped us better identify and manage the safety exposure that comes with this new risk
(SPEECH)
LOUISA DESSON: Certainly, it seems like a lot of peace of mind is really critical there. You mentioned the real time data, how are these wearable devices helping in the construction industry in regards to that real time data?
(DESCRIPTION)
Image, Visualization of construction job site computer dashboard. Motion graphic the details worker data on the dashboard. Text, Know where your workers are and who they’ve been in contact with. Logo, Travelers.
(SPEECH)
DON NABER: You know, for us in that real time data What we're focusing on is first and foremost from an efficiency standpoint, making sure everybody's in the right spot on the construction site. This particular service is not a GPS system that is going to follow you wherever you go. It's triggered once you walk on the site with the clip that's there. And all we care about at Gilbane is making sure that everyone is safe. What happens when people leave the job, obviously, that's not of interest to us and we obviously want to make sure that that's very, very clear. But you know when it comes to the information that's readily available to us, the one thing that we were drawn to this product is the fall detection system that's available.
And I'll allow Bob to go into that the whole system and how it works. But it allows us to give immediate attention to people if and when they're injured on the job site. And there's a whole lot more to the system that I think Bob can do a better job going over.
(DESCRIPTION)
Bob Dolan speaking over slide with his video displayed in top right corner. Visualization is displayed of construction job site computer dashboard. Text, Know where your workers are and who they’ve bene in contact with. Logo, Travelers.
(SPEECH)
BOB DOLAN: For sure, Don, I appreciate it. And I appreciate the kind words about what we do, obviously. Our focus since the inception of the company is to drive safety and enhanced safety on every environment we step on to through the use of the technology. So the spire system again is a real time 900 megahertz network. So we don't use GPS, we don't need Wi Fi, we simply utilize a seamless and easy to deploy network that utilizes a cellular up link to get data to people in real time.
Our devices themselves allow for identification of freefall. They allow for push button alerts so workers can in fact report an injury, they can report a variety of different issues related to reducing risk. So we feel like when it comes to safety, the real time aspect of what we do is so critical because it allows our clients like Gilbane and others to act very appropriately and very quickly based upon a general area of reporting.
We don't say you are in this specific room, we simply say you're on this floor kind of in this zoned area. So it has allowed for rapid response in critical situations and it continues to evolve through input from customers like Gilbane that have allowed us to kind of expand the product and evolve on it within the construction environment.
(SPEECH)
LOUISA DESSON: And how would you say that that wearables help with reducing the frequency of claims or the severity of an accident?
(DESCRIPTION)
Image, sample map showing location of injured worker is displayed with a key and text. A table is displayed on Historical Behavioral Reporting. Text, Wearables can help identify unsafe behaviors. Logo, Travelers.
(SPEECH)
CASEY BANKS: I could jump in there. So our experience to date really indicates there's not a lot of vendors out there that are providing that overall quantitative lost data. Now, in a perfect world, these devices, they’d be plug and play systems, they provide immediate impacts to injury reduction. Reality is that it really depends on the company's level of commitment with the adoption of the technology and not just at the corporate level, but we find at the field level as well. And how they act on the data and analytics from the output of those systems. So what we see is that without a dedicated team structure, process, it's going to be very difficult to see the intended results.
So for example, I deploy proximity sensor technology on a job site and don't have any struck by incidents for six months. Is that a function of the technology working or the company's proactive safety measures or is it a combination of both?
So what I'm saying is, in order to see observable loss reduction trends over time, I really think companies need to work with the vendor to develop KPIs that aren't strictly focused on claim reduction.
But they also have to look at leading indicators, like behavioral risks and near miss data to try to provide more actionable insights, which is what you see on the screen there on the right. Some of the wearables like Triax can help to reduce the accident response time on the job site, which we know overall it'll help expedient the claim, get the person triage, get the claim reported into the carrier. And at the end of the day that benefits all parties involved.
So what you see here on the left is an image from Triax talking about that accident response time and I'll turn it over to you, Don. Maybe you can provide some of the real life examples that Gilbane has had with the technology.
(SPEECH)
DON NABER: Thank you. So, one thing that I would add is obviously all the things you talked about are all the reasons why we want to use this product or technology in general. But a benefit here to is it from a fraud detection standpoint.
Because not only do you understand what, where, and when something occurred from a fall perspective. You also have an understanding of who are the individuals who are around at the time that incident occurred.
So we have the ability to ask questions and investigate in a much more expedient manner than what we might be able to do without the technology because identifying all the people that may have been there without this technology is not always the easiest thing to do.
But this allows us to, like I said, identify whether it was coworkers or whether it was another subcontractor who may have been in the area. This helps us really understand things and determine if a particular accident was something that was staged or if it was something that actually occurred.
So obviously, the most important thing is getting that that quick response to give people the attention that they need, but it's also a tool to help reduce and maybe even eliminate fraud, if it were to happen at the construction site.
The other thing that I wanted to mention in terms of the response time is in some of the examples that we have, one of the projects that we have in Florida, we had an individual who had a very severe cut on their thigh, and not only do you have fault detection in the system, but it also has notification. So a number of people on the site were able to use their notification button to be able to notify our team on their particular project. We had an EMT, and the EMT was able to get out in a very, very short period of time and the people who were immediate to the incident that occurred, they applied a tourniquet. And when the EMT got there, while the tourniquet was helpful, it could have actually if it wasn't changed or adjusted it may have caused maybe some further challenges as well. But this is somebody who actually wound up getting a number of stitches wound up back on the site. The next day, so we didn't even have a loss time with the situation, but the EMT said and the doctor said that had had he not gotten the attention with the tourniquet and so forth, there was a good chance that he would have bled out.
So this obviously provides the value add, and when you think of something like that, it's not about the money. It's about that somebody's life was saved. And while there were great people around, the Triax system brought the right people around at the right time to help solve the problem. So obviously, that's something that is, you know, you just can't put $1 value to that.
(SPEECH)
LOUISA DESSON: Absolutely. Getting the right resources right when you need them, certainly a huge benefit. And there may even also be potential other long-term risks that you're able to discover with some of the data, I would imagine.
(DESCRIPTION)
Don Naber speaking over slide with his video displayed in top right corner. Image of construction worker jumping off construction truck is displayed. Text, Devices reveal hidden dangers. Logo, Travelers.
(SPEECH)
DON NABER: So this is a great picture and one Bob Dolan and I lived at one of our projects where the sensors have adjustments to them in terms of detecting how far somebody may fall, whether it's a foot, whether it's four feet or whatever, and you can adjust the sensor accordingly in the system. And we had it set at a very low level and it was an awful lot of alerts or what we believed were false alerts. And our project team was getting very frustrated by that. So we had Bob and some others from Triax go in and just monitor for the course of the day to see if they can understand what was going on. And what we came to the conclusion of was is that, like this picture, many of the workers were jumping off the back of pickup trucks, supply trucks, they were jumping from one level to another of roughly three or four feet, and that's what was causing the notifications in the system.
When sitting down with the subs and talking to them about, “hey look, this is a repetitive motion problem. This is somebody who's young in the construction industry who has plans to be in it for the rest of their life. This is something that is going to cause problems over time to your knees, your hips, your ankles, etc.” But what came from it really was a bigger view than that which that's an important view. But one of the reasons that they were doing it is because they felt that the way that the project and the site was laid out didn't give them all the access points that they needed. So they were taking shortcuts and those shortcuts required jumping in certain areas and cutting corners. So it helped the communication with the project team to reduce overall exposures at the site so not only were we getting rid of the immediate claim or incident circumstance, but we're also taking care of some of the long term wear and tear that could occur.
But at the same time, we're also fixing and enhancing the overall efficiency of the job by creating better access points for the workers.
(SPEECH)
LOUISA DESSON: That's a great story, it really highlights the importance of the communication between Gilbane and Triax and recalibrating the technology and really figuring out exactly what's going on there. Not just dismissing those as false warnings and really seeing what the data is telling you.
So when we think about these devices, we talked a little bit about the monitoring of employees, are there any employee privacy concerns that companies should be aware of when implementing wearables?
(DESCRIPTION)
Casey Banks speaking over slide with his video displayed in top right corner. Text, Data and Security Considerations. Logo, Travelers. Two images are shown regarding Transparency and Cyber Security. Text following images.
(SPEECH)
CASEY BANKS: So employee privacy, I mean, that's always a consideration, should always be a consideration. Anytime we're selecting a specific vendor or product, one aspect is really understanding what the data captures and what it does not capture. And the issue here is that, and Dawn talked about it a little bit, workers could be apprehensive about potential negative consequences related to that data that's collected about their activities, especially wearables that track job site movement, locations. So from that aspect, transparency matters.
It's always helpful to show sample outputs before that wearable project begins and then throughout the project as you go along, provide that information to those workers.
So just to help confirm that the data is being used for its intended safety goals and we're not trying to track that work or when they leave the job site.
Another concern is how privacy is preserved through the vendors use and management of that data that you're providing them. So it is common with a lot of these vendors that personally identifiable information such as name, gender, age is used in conjunction with other data points to try to identify and look at insights into trends.
Some of the things you want to find out from the vendors and some of the things you want to ask is how they protect the data while it's in their use and whether they keep it, whether they share that resulting data to third parties, which in some cases they might actually do that. So that's always a question you want to find out. Encryption practices, removing that personally identifiable information, I think that's pretty normal process among a lot of the vendors out there, but we really can't assume that the proper levels of data security, privacy measures are in place.
So find out that information and that should overall that should be part of that vetting process with any perspective vendor that that the companies looking to hire use the technology. So, always ask those questions.
And really to summarize the points and to drive home these points here. You want to understand how each technology, vendor specific product not only captures the information and data, but also how it shares, stores, analyzes, and protects that data as well. Because at the end of the day, you want to make sure it's secure. You want to make sure that it's in the right hands.
So transparency is critical with not only your staff but if you have other subcontractors, if you have owners involved with that technology, you want to make sure that you keep them up to speed on what's going on and how that vendor is or isn't using your data.
(SPEECH)
LOUISA DESSON: Those are great points. And it sounds like communicating that it's not intended to be big brother, but safety and productivity go a long way.
(SPEECH)
BOB DOLAN: Yeah so you know, Casey's point, I think one of the things that we tried to do at every single one of our projects, but I know work very closely with the Gilbane teams around the country, is to be totally transparent with any type of work.
They have questions, we want to give them the honest answers and be totally transparent. People look at sensors sometimes, and they say, well, we're being tracked. We often get into a pretty lengthy discussion about the fact that we don't use GPS, and I have no problem tearing open a sensor if I had to, to show there's no GPS technology in this.
And oftentimes, I've had to prove to people that set up a small network, I walk outside the network, I disappear. So I just think that Casey, to your point being really transparent with people, answering their questions ,the fact that we use a radio frequency, not a phone-based app which we have GPS involved in it, we do not use any of that.
So we really try to address those privacy concerns with the workers to make them feel comfortable that really what we're doing is providing them a tool for their use and to enhance safety so they get home every night.
(SPEECH)
DON NABER: And Bob and I have met with a number of the unions around the country on this very issue. Obviously the unions are protecting their workforce and we clearly respect that and our goal is to show them that this is about protecting the workforce as well by providing a safer work site, not to get into some of these lives from a data perspective, that's not of interest to us.
But to Bob's point, and sitting down and having the conversations and helping people understand what the system does, it goes a long way. And it has allowed us to use the product and the service from a technology standpoint in areas where we felt that we were going to really struggle. And when Bob and I reached out to our project teams and said, hey, look, can you just give us a little bit of time in front of the workforce to explain it, and their leadership. And when that happened and we were able to do it, it clearly paid dividends and allowed us to go forward, and many of the unions are very interested in the product and want to try and understand more about what the data can do for them.
(SPEECH)
LOUISA DESSON: That's great. And I think when you can share success stories like some of the ones that you've shared today where they impacted real employees, that can go a long way as well.
So certainly we've seen enormous transformations over the past eight months or so with COVID and the use of wearables.
A year from now, what do you think the construction site of the future will look like? And are there practices and wearables that will become the norm?
(DESCRIPTION)
Don Naber speaking over slide with his video displayed in top right corner. Three images are displayed of construction workers in the field. Slide title: Construction Sites Over Time. Text per image: Past, Present, Future. Logo, Travelers.
(SPEECH)
DON NABER: I'm just going to move to the, the right hand side of that. And for us, the future is noq. That is a picture from one of our job sites that was provided the other day. And it's integrating a number of different technologies together to establish an access point but also address some of the concerns that we're having from a COVID standpoint.
So this gentleman who is in the picture on the left side, you can see that he has a mask on. And what the white box that he's looking at is actually a temperature detecting system that is taking his temperature, but it's also verifying that he has a mask on, which is one of the requirements of the job that he's on. This happens to be in the state of New York.
And once that's verified that his temperature is acceptable and obviously verifies the mask, he has his Triax Spot-R clip on and what happens is that now that the turnstile that you can kind of see there notifies the turnstile that that the person who just had had done the temperature screen, is going to be coming through.
So he has to take his clip out, lets it activates the turnstile for about 10 seconds and then the clip will open up the turnstile. So we've done a number of things here in terms of the access point. We've taken care of the temperature, we verified the mask, now we've identified who's going on to the site and we've kept the site protected from people walking on or leaving the site because when you leave you actually have to clip out, too, so now we know who's left the site as well.
So technology has done a wonderful thing in terms of helping improve access points in control of who does and who does not go on to the job.
(SPEECH)
LOUISA DESSON: That's terrific from a security standpoint as well as a safety point of view.
How about Bob, any predictions?
BOB DOLAN: As technology gets infused into these construction sites at a variety of different levels and we're starting to see it already, where users are already seeing benefit from having open API architecture and the ability to integrate other best to breed technologies to provide data. And we're seeing that every day, so what we're trying to do as a company is not only aggregate, integrate, and communicate that data to a simple dashboard, where they can see it and act on it in real time. So those day-to-day decisions are utilizing multiple technologies, they're sitting in one place, they can be viewed from multiple areas as long as you have an internet connection. You don't have to be at the job and you can start to see trends emerge and address them early on as a leading indicator versus lagging and I just see that constantly continuing.
I mean, it started for us with a simple integration with Pro core. We took what we do, headcount some safety information and push that across to the pro core platform that allowed them to automate, truly automate without touching or entering into an application headcount and any type of safety event, that gets automatically pushed over.
The second example was the one that Do just gave you at the New York site and that was driven by the project team. They asked us to collaborate with them to see if we could meet that need and reduce bottleneck at thermo temperature at the gate, and we were able to do that. We're happy to do that.
It's all in different ways to integrate different technologies, leverage other technology to solve real problems and create the value that project teams absolutely desire.
So I see that happening more frequently. We continually have greater buy-in from executive level. And when we are able to show those values at the project level, people really adopt very quickly.
(SPEECH)
LOUISA DESSON: That's great answers, being able to take action with the data right away is really a tremendous move forward rather than having to take it away and interpret it just having it be fashionable in real time can really help keep folks safe.
So as we look at construction companies that might be interested in getting a wearable technology program off the ground, what recommendations might you all have?
(DESCRIPTION)
Casey talks over slide. Four graphic images are displayed with corresponding text. Logo, Travelers. Text, Four key steps when launching a wearables program. Have a strategy. Know what you’re getting into upfront. Factor in cost implementation. Test, learn and repeat.
(SPEECH)
CASEY BANKS: And this really goes back to the original comment I made about asking yourself, what's the problem you're trying to solve with the use of this technology. So whether your focus is accident frequency, it could be leading accident causes, it could be financial pain points within the company. You want to understand the nature of your losses and your claims, where they’re coming from, and then look at what the solutions are. And that's really going to help you develop a solid strategy for trying to engage a suitable technology vendor.
Know what you're getting into up front. Make sure your company is willing to put the time and resources to oversee the initiative and I think this is critical. This could involve having a dedicated team and even a dedicated budget to account for all the costs involved with that program and all that data analysis that comes along with that technology that you might not really be prepared for or used to getting.
Lean on the resources around you so insurance carriers, other contractors, look for some guidance from them and try to get some unbiased feedback on the technology effectiveness. So there's other companies that have used technology in the past, find out how it's worked for them. Talk to your insurance carrier, see if they have any input, if they have any recommendations, what their experience has been. And really think about the relationship with the vendor as more of a partnership. So you really want a lot of communication there. They should be actively involved in the program throughout the whole process and from the beginning they should help you in developing those key performance indicators, those KPIs for that project. And finally, I would say have a process to monitor, evaluate, adjust throughout that pilot program. And consider developing if you have lessons learned at the end of all this, consider developing those and sharing those internally, sharing them with the project team, and even putting together a technology playbook. So you want to make sure you outline the process, the expectations, so was it effective, and then moving forward if you end up using that technology again, or you use other technology, you already have a set of expectations and guidelines on how the company really needs to move forward with implementing it.
(DESCRIPTION)
Louisa talks over slide. Four graphic images are displayed with corresponding text. Logo, Travelers. Text, Four key steps when launching a wearables program. Have a strategy. Know what you’re getting into upfront. Factor in cost implementation. Test, learn and repeat.
(SPEECH)
LOUISA DESSON: It's really good actionable advice from having lived it. Any advice, Don, in the field?
(DESCRIPTION)
Don talks over slide. Four graphic images are displayed with corresponding text. Logo, Travelers. Text, Four key steps when launching a wearables program. Have a strategy. Know what you’re getting into upfront. Factor in cost implementation. Test, learn and repeat.
(SPEECH)
DON NABER: Thanks Louisa. Casey is just spot on in terms of the direction. And the one thing that I would add is that, many times there's all these different opportunities that are available to us in so many ways from a technology standpoint.
The one thing that we've done at Gilbane is as we get access to or are made aware of certain technologies, we look at it as relates to our company strategy, our core values. And is the technology, does it tie into who we are? If it obviously can improve who we are, that's a great thing. But if all of a sudden, it starts adjusting what our strategy is or what our core values are or fundamentally what we want to do as an organization, we really need to take a step back and say, is this really a direction that we want to go? The core values of Gilbane and the strategy, and while the strategy adjusts and so forth, those core values remain consistent year in and year out. And I would say that when we look at whether its technology or whether it's other services, we're trying to make sure that those items match up well to who we are and what we want to try and accomplish. We don't want to change who we are, because of technology.
(DESCRIPTION)
Louisa talks over slide. Four graphic images are displayed with corresponding text. Logo, Travelers. Text, Four key steps when launching a wearables program. Have a strategy. Know what you’re getting into upfront. Factor in cost implementation. Test, learn and repeat.
(SPEECH)
LOUISA DESSON: That's great. I think that being transparent with your workers, learning from the data, knowing what type of problem you're trying to solve; certainly some key takeaways. Bob any insights from being on the Triax side of the equation? Things that you wish companies would know?
(DESCRIPTION)
Bob talks over slide. Four graphic images are displayed with corresponding text. Logo, Travelers. Text, Four key steps when launching a wearables program. Have a strategy. Know what you’re getting into upfront. Factor in cost implementation. Test, learn and repeat.
(SPEECH)
BOB DOLAN: I couldn't really have said it much better from then Casey and Don said it, but I will add one other piece of it. If it's an initial project, pick the right project. It doesn't have to be the biggest project. In fact, I would maintain that the first project should be appropriately sized. Big enough that you'll get meaningful data but small enough to show value and to the project team and then you can build off because in my world success breeds success.
The first project we did with Gilbane was not a huge project. It was a small project and we had some success. We also had challenges that we're able to deal with on a smaller scale. So I think one of the things that I would urge people to do is if you're looking at technology, make sure you pick the right project, it aligns with the corporate initiatives, pick the right project team. Those general contractors, the CMs, they know exactly who is engaged with technology, who wants it, and thirst for it because they're asking technology organization within a Gilbane “what can you do for me here” in terms of discovery. So I think that is one of the biggest things that we see is the right size project, the right team, that's well aligned.
The last thing I would say is to try to be as articulate and as honest with what the technology can do for the organization and for the project team on the ground and set the realistic expectations.
So, you know, those are really where we've seen success and we've been able to build off success has been when we've appropriately set the expectation, picked the right project, had good alignment with the with the corporate initiatives, and the correct project teams.
(DESCRIPTION)
Louisa talks over slide. Four graphic images are displayed with corresponding text. Logo, Travelers. Text, Four key steps when launching a wearables program. Have a strategy. Know what you’re getting into upfront. Factor in cost implementation. Test, learn and repeat.
(SPEECH)
LOUISA DESSON: That's great. Well, thank you all for your answers to this we will turn to questions now. And there's still time to ask your questions in the Q and A box here.
(DESCRIPTION)
Louisa speaking over slide. Text, Q&A. Image of individual pointing to watch as slide background.
(SPEECH)
LOUISA DESSON: And this first one is for Casey. So you referenced what problem are you trying to solve. What if the construction company doesn't know what specific problem they might be tackling, how do they how do they get a handle on that? And you know if there's something that's more long term, how would you advise them to kind of look at their options for wearables?
(DESCRIPTION)
Casey speaking into camera.
(SPEECH)
CASEY BANKS: Yeah so if you look at it and you look at the problems you're having internally or I mentioned earlier as an industry we are seeing a lot of issues around lack of skilled labor, we are seeing an aging workforce, a multi generational workforce. So kind of look at the broader picture and see where there might be opportunities to incorporate technology into your current risk management programs to try to address some of that. And then look at the losses.
What do you have for losses? Where are your trends coming from? What kind of claims do you have? What are some of the issues you're having out on the job site? Are there behavioral issues that you feel like could be addressed through the use of different technology?
And then at the end of the day, if you look at it and you say, you know what, we don't have problems, everything's running smoothly, we don't feel the need for it, then maybe it's just, it's not the right time. And, you know, we don't want to force ourselves into the use of the technology so if we feel like things are running smoothly and we feel like there's not a need for it at this point in time, then I think it's okay to step back and say, it's just not right for us.
(DESCRIPTION)
Don speaking into camera.
(SPEECH)
DON NABER: Now, I think it's a really good point, Casey. You know when it comes to the technology, if you don't necessarily understand what the problem is to solve, its to really sit down and look at certain things like your data and so forth and say, okay, is this something that we can fix and what can technology do to help that? I think that's a lot of what we're doing right now. We have a lot of data that's available to us. And the interesting thing is that as you go through the data and you start having conversations with people within the organization, they may have a very different understanding of what that data means. And you find things out and what you thought was the proximate cause of an issue wasn't necessarily. So for example, you look at housekeeping in general and say, well, geez slip, trip, and falls come from housekeeping issues. Well that is true. But when you kind of look back at the proximate cause of it, did the people have the right training? Did you have the right subs who focused on what they were supposed to do? So those are some things that lent to the issue of the housekeeping. So what Casey's explaining makes all the sense in the world and there's a lot of data that's available to understand a lot of different things, but really drilling down on that data, I think will help you lead to some answers in terms of what you need.
(DESCRIPTION)
Louisa speaking into camera.
(SPEECH)
LOUISA DESSON: I think Bob's observation to starting small, you might not tackle the biggest problem your organization is having. You can start with something that you can measure and then you might have a meaningful look at whether or not the technology is helping you solve even a small problem.
But very, very interesting. So thanks to whoever asked that one.
How can we use these technologies and horizontal construction when there's no or weak internet connection available? And sometimes they are projects that are several miles from the field office to work to work distance in miles.
(DESCRIPTION)
Bob speaking into camera.
(SPEECH)
BOB DOLAN: Sure and that is a great question. I'm glad it was asked.
With our technology, we don't require Wi Fi. I simply need to have cell signal to drive that data to the cloud. So most every site we've been on in some of the most remote areas, we've had difficulty for other technical reasons. But the reality of it is there's a variety of different ways to get data to where you want it to go, which is into the hands of the client. And we utilize a cellular signal to drive that data to the cloud. So I think a lot of technologies will require some level of Wi Fi; we do not. So I hope that answers the question.
(DESCRIPTION)
Louisa speaking into camera.
(SPEECH)
LOUISA DESSON: That's great, thank you. And the next question I'll open to all of you, how specifically can wearables help prevent fall risks?
(DESCRIPTION)
Don speaking into camera.
(SPEECH)
DON NABER: I don't know if it can prevent the fall risk and I don't think that's really the intention of it. What's going to really prevent the fall risk is obviously making sure from a training perspective, you've got the right training, the subcontractors who are coming to the site have the right equipment. You know obviously we have a feeling about ladders on our project sites that we believe that there's other ways to be able to access heights versus ladders. But the system itself is obviously giving us the opportunity to get to somebody who did fall and I think what it also does is that if there is a fall and hopefully that person was not hurt, that you can learn from that fall and what the circumstance were around from that and make sure that that same terms type of situation doesn't repeat itself. So I would say can it help you in terms of preventing falls going forward in terms of what you learn? Absolutely. But it's really that training of the people who are coming on to the site and the subcontractors who are working there, to me is obviously the best prevention. But obviously we learn from our mistakes and that the Triax system helps us kind of understand those falls and when they happen so that way we can investigate it right away and get a better understanding so that way we can prevent it from going forward.
(DESCRIPTION)
Casey speaking into camera.
(SPEECH)
CASEY BANKS: I would also say that with the system, it does help look at leading indicators. So it does look at observable behavior. So, and Bob can talk a little more about this, but one of the slides you saw the green and red graph on the right side of the slides, it's showing behaviors that are happening on the job sites. So over time, you're starting to see those near misses. You're seeing people maybe jump off the tailgate, you're seeing people jump off ladders, where it's not a claim, it's not an accident. But if you start to bubble up all that data and you can identify, okay we have a couple workers here who continue to have these what we call low height activity events, we need to go have a conversation because even though we don't have an actual fall yet, that behavior eventually tells us it's going to lead to an accident. But, Bob, and I'll let you explain that a little better.
(DESCRIPTION)
Bob speaking into camera.
(SPEECH)
BOB DOLAN: Sure, the sensor itself detects free fall. As I mentioned earlier, we measure everything from 18 inches up. We alert automatically at six feet of freefall. So we collect everything, we look at everything and we can compare across a job site, multiple job sites, and take a look at that what Casey refers to is low, high P or behavioral report. So not everybody is falling or there's not five footfalls or four footfalls. But we do see a lot of little things happen that are as Casey indicated a leading indicator of what could happen down the road.
So the purpose of that report is simply to again push some actionable data into the safety coordinators of superintendents’ hands. So maybe it's stretching flex, we're talking about something specific to, hey listen we're at this stage of the of the job right now, we want to be aware to take your time going downstairs. We see a lot of low height activity when stairs go into a building.
So, everybody is in a hurry on a Friday afternoon to get home, that three step job may not seem like much, but it can result in a twisted knee, arranged ankle or whatever it may be. So we're trying to drive that data to where it can make a difference long term and change behaviors, frankly.
(DESCRIPTION)
Louisa speaking into camera.
(SPEECH)
LOUISA DESSON: That's great. Last question is in regards to real time data. Data is just data until analysis happens. Can you talk more about how you're breaking that data down to make it more actionable?
(DESCRIPTION)
Bob speaking into camera.
(SPEECH)
BOB DOLAN: Sure, we utilize product from Amazon Web Services called quick site, which allows us to aggregate, compare, and push data or make it available via a simple dashboard. You can export anything that we collect into a BI environment so you know what we're seeing through our open API. A lot of people will take that, export that data into their environment, and put some analysis on it that they that they want to perform. We do work with, we do have a data scientist on staff.
So we often will have that individual contact a client who's asking for something very specific and we'll build a dashboard around it to try to meet that need. And as I said, we use the Amazon Web Services product called quick side.
(DESCRIPTION)
Louisa speaking into camera.
(SPEECH)
LOUISA DESSON: The more you know what problem you're trying to solve, the more you can look at that data to solve that particular problem .
(DESCRIPTION)
Bob speaking into camera.
(SPEECH)
BOB DOLAN: And just to give you a simple example. I mean with our system, because it's real time and because I we can identify arrival and departure, regardless of the presence of a turnstile, I can look at compliance to entry and exit to a job site. Our device can act as a credential, but if a worker should leave through a side door. I'm going to see that person disappear without an exit. So that gives me some insights, that gives me some value as it relates to security to a building.
(DESCRIPTION)
Don speaking into camera.
(SPEECH)
DON NABER: Much like Bob, and I know Travelers does the same, we have the ability to take data from all different sources. So we're actually taking data from Triax, we're taking data from predictive solutions, which is a site evaluation process that we go through, our incident reports, and then we're also taking our lost data from our claims and we're pulling that all together. And we're kind of overlaying it to kind of look at, are the things that we're seeing from an immediate standpoint to the incidents that happen from our reports and then the claims that are occurring, is there consistency? And if there's consistency it's a really easy thing to try and figure out how you manage it. But if there's an inconsistency, then it allows us to kind of look at the data a little bit different to say, well, wait a second, we're having these kind of losses. But from an observation standpoint, we have this, this, and this. So it allows us to go back and say, are we looking at the right things as we're looking at the job? Are we utilizing the data that comes from Triax the right way.
So now we have a broader perspective of where we need to focus our attention and some of it, like I said, is how we observe things. And obviously, some of it is how we prevent things. So we actually have a data analyst who's on staff with us, who is taking all this data, putting it together and creating dashboards so that way we can share it with the job, we can share with a business unit and we can share with individuals. So that way, from a training perspective, we know where they need to focus their attention.
(DESCRIPTION)
Louisa speaking into camera.
(SPEECH)
LOUISA DESSON: That's great. Well just tremendous potential for this technology from a safety standpoint, certainly with COVID-19 and also an efficiency and productivity standpoint. So thank you all. Don and Bob and Casey for taking the time and for all of our participants.
For more information, you can contact your Travelers representative or visit us at travelers.com for lots of great safety content. So thank you all and take care.
[MUSIC PLAYING]
(DESCRIPTON)
Travelers Logo