Helping Equipment Breakdown Policyholders Mitigate BIL-Related Risks
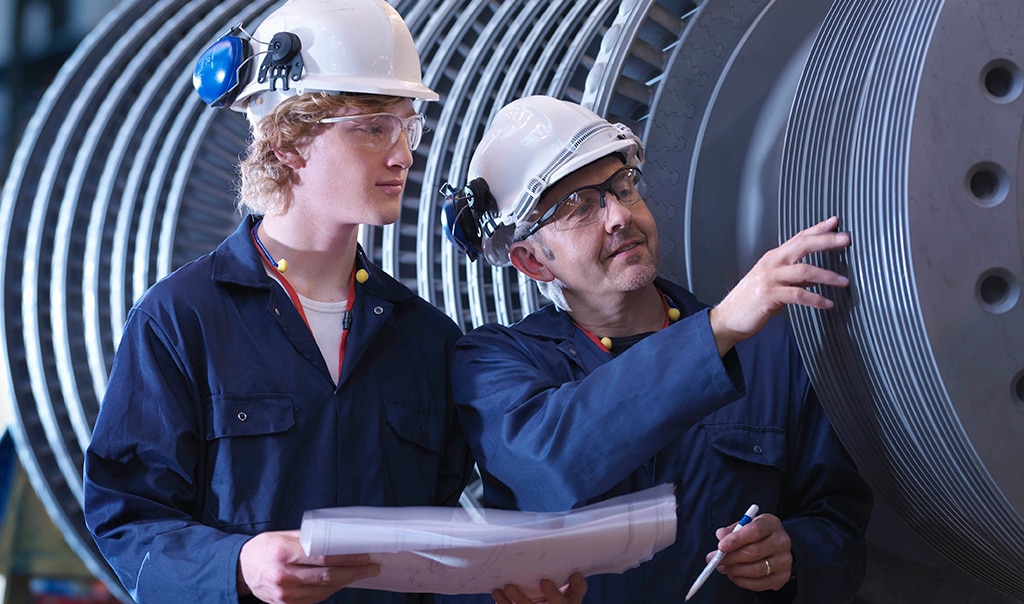
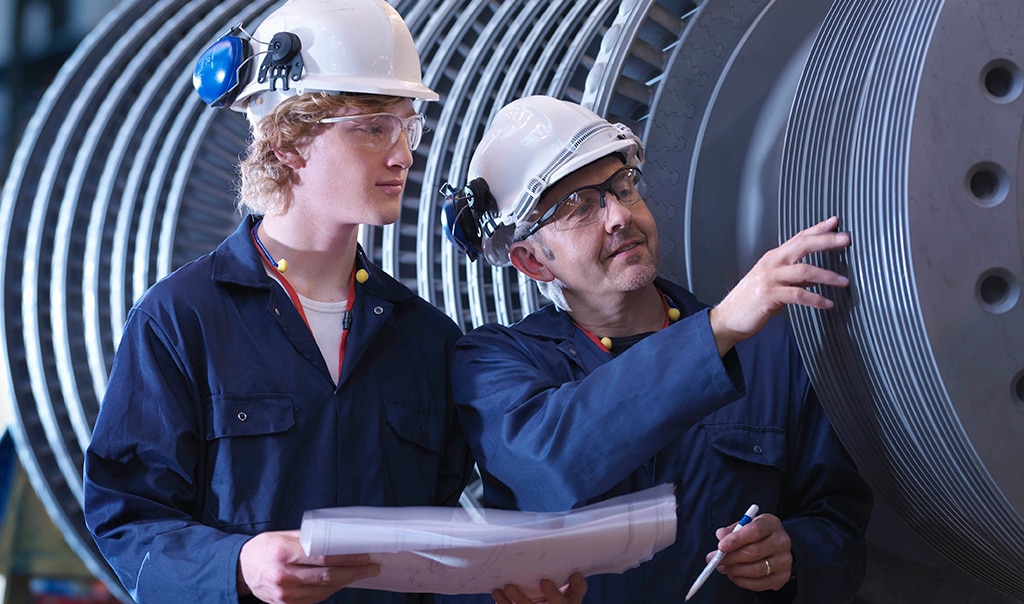
Great optimism has come with the passing of the Bipartisan Infrastructure Law (BIL). This is particularly the case for a business looking to capitalize on its potential for more work. As a provider of equipment breakdown coverage, you need to be aware of the potential impact the infrastructure law could have on your book of business.
Many experts, including BoilerRe’s National Director, Jim Jarvis, believe existing supply chain disruptions, skilled labor shortages and power quality issues may worsen as work on American infrastructure begins. This could leave equipment and machinery owners – and potentially, those who insure them – increasingly susceptible to escalating financial impacts of equipment breakdowns. Even for equipment owners and insurers not directly involved, the potential impact of BIL-funded projects remains. Why?
The cost and time to acquire, maintain and repair equipment could escalate as demand for critical components and trained technicians to support infrastructure work grows. Meanwhile, more equipment-damaging electrical spikes, surges, dips and arcs may occur within our nation’s electrical grid under the added pressure to power BIL-funded projects. These conditions could create a perfect storm where equipment breakdowns are more likely to occur and result in longer downtime and higher claim costs.
If equipment and machinery owners fail to protect their operations from the risks associated with these unprecedented supply chain, workforce and power reliability challenges, increased costs could result.
The coverages you offer can be an important safety net, but preventing equipment breakdowns in the first place is always the best risk management strategy for equipment owners and their insurers. Providing the guidance equipment owners and operators need to stay one step ahead of anticipated BIL-related challenges can add value to the protection you offer and strengthen relationships with those you insure.
Travelers BoilerRe leaders share their advice to assist you in helping your equipment breakdown policyholders manage the risks associated with owning and operating machinery, now and into the future.
Overcoming Workforce Challenges
Attracting and retaining qualified technicians to operate, maintain and repair equipment and machinery can be difficult even under normal conditions. Existing and expected labor shortages due to the influx of BIL-funded projects may make it more important than ever. Advise the machinery and equipment owners you insure to:
- Offer competitive compensation and benefits packages. Attracting and retaining employees can be challenging in a tight labor market. Offering competitive salaries, bonuses and benefits packages can help the equipment and machinery owners you insure stand out and attract top talent.
- Automate or outsource tasks. If policyholders are unable to find labor in-house, automating or outsourcing certain tasks to third-party vendors may be an effective way to manage workloads – particularly if they are struggling to find skilled workers for specific operational and maintenance tasks.
- Train current employees to develop existing skills or learn new ones. Encourage the equipment owners you cover to invest in the employees they already have! Providing training and education to staff can help maintain their internal supply of skilled labor, improve retention rates and increase the overall effectiveness and efficiency of operations.
- Partner with local schools and vocational programs. Working with educators running vocational programs to identify and recruit the top talent entering the workforce can help equipment owners and operators build a reliable pipeline of skilled workers for their current and future needs.
Overcoming Supply Chain Disruptions, Labor Shortages and Power Reliability Issues
Keeping machinery and equipment running, particularly when essential parts, skilled labor and reliable power are in short supply, can be challenging. As work on American infrastructure begins, increased stress on the system could make it even harder. Controlling the risk is key to preventing equipment breakdowns or minimizing the impact should one occur. Remind and help your equipment breakdown policyholders to:
- Proactively plan to help mitigate the risks associated with supply shortages and delivery disruptions.
- Keep an eye on market trends and industry forecasts. Both you and your policyholders should stay up to date on the availability and prices of materials and equipment, as well as any geopolitical events impacting raw materials providers, to anticipate shortages and plan accordingly.
- Consider alternative materials or equipment. If a critical part or piece of equipment is in short supply, advise policyholders to consider alternative options that could serve the same purpose – yet be mindful of how these work-arounds could impact their warranties and insurance coverage terms and limits.
- Build relationships with multiple suppliers and service providers. Ensure that policyholders understand the importance of establishing a geographically diverse vendor base. Help them to build and maintain relationships with backup suppliers they can work with in the event that their primary suppliers experience a disruption.
- Stockpile critical parts and equipment. Policyholders should keep a sufficient supply of their most important machines and components on hand to ensure that they can continue to meet demand – advise them to be practical, considering any inventory or budget implications.
- Increase production and optimize use of available supplies. When possible, encourage policyholders to ramp up production of products made with machines or materials that may be in short supply – and help them look for creative ways to maximize output from available supplies when limited.
Fortify power generation and delivery systems to minimize the frequency and impact of electrical surges and power outages.
- Upgrade outdated electrical components and systems. Encourage policyholders to make necessary improvements to increase the reliability and capacity of their power sources. Urge them to regularly perform routine inspections to identify and address potential issues before they cause damage.
- Implement backup power systems. Advise policyholders to install generators and battery-powered backup systems, like an uninterruptible power supply, or UPS, to ensure that all critical machines and equipment can continue to operate in the event of a power failure.
- Monitor power quality. Recommend the use of power monitors to policyholders. This will enable them to track power quality in real time, ensuring they can identify and address issues as they arise to help prevent failures or damage to equipment and parts.
- Optimize energy usage. Suggest that policyholders install power management systems to help optimize the use of electrical power. Advise them to make necessary modifications to reduce overall demand on their electrical infrastructure, as necessary.
Prioritize maintenance to keep machinery and equipment in top shape and less susceptible to breakdowns.
- Implement a preventive maintenance program. Ensure that policyholders inspect, clean and repair critical machines on a consistent schedule. Help them set clear goals for their maintenance plan and assist them in reviewing and updating it regularly so that it remains effective.
- Invest in skilled maintenance staff or train existing employees. Advise policyholders to put experienced technicians on their payroll or train current employees to take on critical maintenance tasks, providing access to education so they maintain the skills and knowledge to properly service equipment.
- Use predictive maintenance technologies. Encourage policyholders to leverage tools, like vibration monitoring and thermal imaging, to help identify potential equipment failures before they occur, allowing for staff to make timely maintenance and repairs.
- Outsource machine maintenance, when necessary. Recommend using a third-party provider for critical maintenance and repairs to supplement internal capabilities – encouraging policyholders to carefully vet vendors to ensure that they have the required skills and expertise.
BoilerRe has been in the business for more than 100 years. BoilerRe couples innovative equipment breakdown reinsurance solutions with industry-leading expertise to help equipment breakdown insurance providers proactively manage underwriting risk.
To learn more about the many ways we can help you and the policyholders you insure mitigate existing and emerging equipment breakdown risk, contact your dedicated BoilerRe client services manager today.
Sources
H.R.3684 – Infrastructure Investment and Jobs Act, 117th Congress (2021-2022) – https://www.congress.gov/bill/117th-congress/house-bill/3684/text
Whitehouse.gov content, “Build Back Better” – https://www.whitehouse.gov/build
A Guidebook to the Bipartisan Infrastructure Law for State, Local, Tribal, and Territorial Governments, and other Partners, May 2022 – https://www.whitehouse.gov/wp-content/uploads/2022/05/BUILDING-A-BETTER-AMERICA-V2.pdf
Fact Sheet: Securing a Made in America Supply Chain for Critical Minerals, Feb. 22, 2022 – https://www.whitehouse.gov/briefing-room/statements-releases/2022/02/22/fact-sheet-securing-a-made-in-america-supply-chain-for-critical-minerals
Travelers Institute Webinar: Insuring the Rebuilding of America: What’s in the $1.2 Trillion Infrastructure Law? What Will It Mean for the U.S. Economy?, Travelers Institute, Dec. 15, 2021 – https://www.travelers.com/travelers-institute/webinar-series/symposia-series/infrastructure
More Trending Topics to Explore
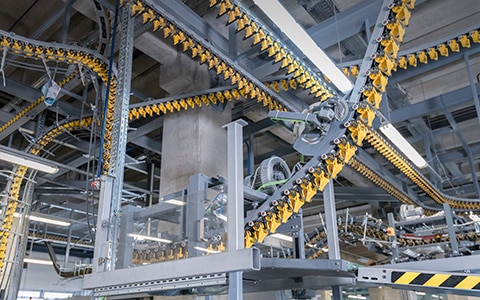
Equipment Breakdown and Supply Risks of BIL Projects
Equipment breakdown insurers may see claim frequency and costs rise if demand for the resources increases.
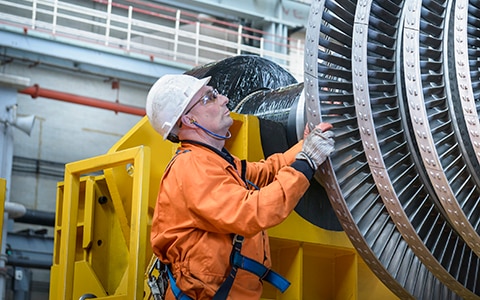
Loss of Skilled Labor to BIL Projects Poses Workforce Risk
Here’s what you should know and do to manage the potential equipment impacts to skilled labor from the Infrastructure Law.