Mitigating Construction Defects with a Quality Control Program
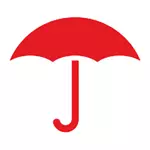
(DESCRIPTION)
Logo, Travelers. Text, Managing Costly Construction Defect Risks.
(SPEECH)
With so many moving parts, it's no wonder you're building projects could potentially suffer costly construction defects, issues that could end up as your liabilities.
(DESCRIPTION)
White construction themed icons within red boxes shift around centered Text, Design flaws. Poor workmanship. Inferior materials.
(SPEECH)
The first step to helping minimize the potential for construction defects is a solid quality control program.
(DESCRIPTION)
Text, Quality Control Program. References, Licenses, Experience, Qualifications.
(SPEECH)
Are you checking references, licenses, experience, and qualifications before bringing subcontractors on the job?
(DESCRIPTION)
A red magnifying glass transforms into a question mark and then a check mark. Text, Management Commitment and Responsibility, Materials Selection, Quality Inspection, Design and Codes.
(SPEECH)
Do you have effective program administration to address key job factors, such as management commitment and responsibility, material selection, quality inspections and design and codes?
And what about a contractual risk transfer program by reviewing and recommending contract requirements, insurance coverage specifications, and indemnification agreements? It can help protect you against a liability caused by a subcontractor.
(DESCRIPTION)
A red ball rolls down a hill, picking up speed and avoiding pitfalls.
(SPEECH)
But even the best quality control program may not be enough. Travelers, resources, and capabilities are here to help. Eligible Travelers customers can take advantage of discounted pricing with a fully vetted partnership in construction management software to help manage your quality control program.
(DESCRIPTION)
White icons of a U.S. dollar sign and a handshake appear in red circles. They rise to reveal a claim document, which is then replaced by graphics of two Travelers employees with speech bubbles.
(SPEECH)
And if an alleged defect does occur and a claim arises, count on the Travelers forensics lab to help determine the cause of the loss. Our claim professionals can help you pursue contractual risk transfer so the correct party bears the responsibility.
Keeping construction defects at a minimum requires maximum care. The pros the Travelers are here to help with services coverages and expertise that can make all the difference. To learn more, talk to your independent agent or visit us at travelers.com/constructionqcplan.
(DESCRIPTION)
Logo, Travelers. Text, To learn more, talk to your independent agent or visit us at travelers.com/ConstructionQCPlan.
Discounts may vary by state and individual risk characteristics. Discounts are subject to eligibility, availability, do not apply to all coverages, and are not guaranteed.
Copyright 2023 The Travelers Indemnity Company. All rights reserved. This material does not amend, or otherwise affect, the provisions or coverages of any insurance policy or bond issued by Travelers. It is not a representation that coverage does or does not exist for any particular claim or loss under any such policy or bond. Coverage depends on the facts and circumstances involved in the claim or loss, all applicable policy or bond provisions, and any applicable law. Availability of coverage referenced in this document can depend on underwriting qualifications and state regulations.
With every project comes the potential exposure to construction defect losses. Having a quality assurance/quality control (QA/QC) program, however, can help reduce this exposure. Three program elements to consider are: program administration and documentation, a subcontractor selection process and contractual risk transfer (CRT).
Program administration and documentation
A number of factors comprise program administration and documentation, such as management commitment and responsibility, design and codes, and documentation, to name a few.
Management commitment and responsibility
Your program should begin with management commitment and include responsibility for program administration and enforcement. A few considerations include:
- A written QA/QC program, signed by the head of your company.
- A plan, time and budget to implement/support the program.
- Individuals with QA/QC responsibilities and accountability.
- A formal commissioning/property transfer program with the project owner.
Materials
Material selection, storage and handling should include inspection, evaluation and documentation/retention confirming that materials comply with building codes, design specifications and national standards. This should be done both before and after installation. A few additional considerations include:
- Understanding new technologies, materials and work methods.
- Understanding manufacturers’ warnings and instructions.
- An acceptance inspection by the supplier, if available.
- Notification process to the supplier if defects are identified.
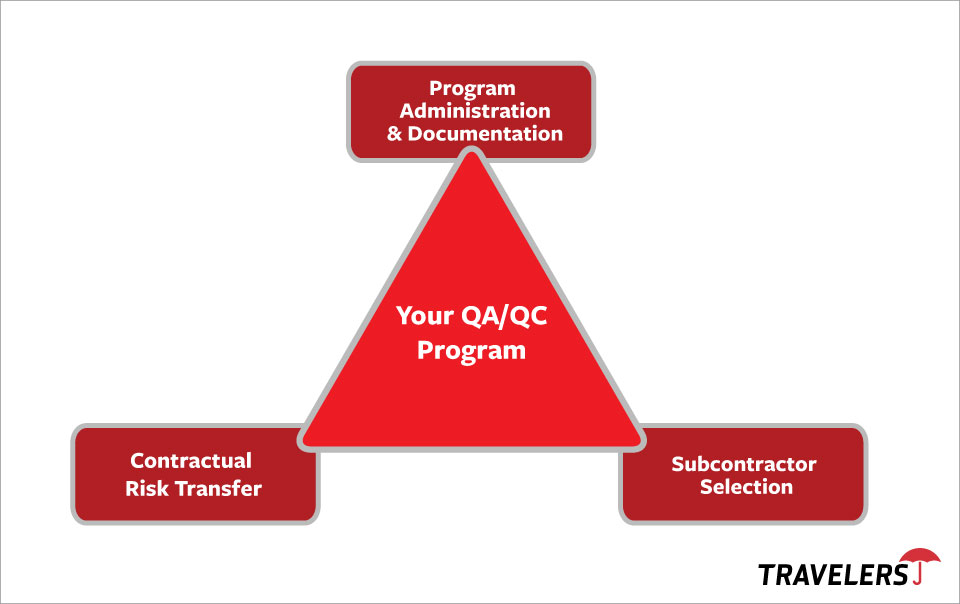
Design and codes
A complete and final approved set of current contract drawings and specifications, including design changes, should be in hand before work begins. Be sure to include building codes for your jurisdiction and accepted engineering best practices.
Quality inspections
Installations should be reviewed, tested, approved and documented. The person inspecting (you, the subcontractor or a third-party inspector) must be qualified to make the inspection and should do so at several phases, including:
- Prior to start of a project or task.
- During the installation process.
- When there are changes in the project, process or materials.
- When the project is complete.
- Upon warranty expiration.
Workmanship
Following the latest approved design documents, product/manufacturer directions and using specified and approved materials can help the quality of the workmanship. Do not substitute materials unless the substitutions are approved by the design team in writing.
Documentation and retention of documentation
Many types of documents are created in the course of a project. Thorough documentation, including of verbal changes and retention of the documents, can play an important role in the event of a construction defect loss, which may occur years later. A common mistake is not fully documenting verbal changes made in the field. Consult legal counsel for state retention requirements where your project exists.
Subcontractor evaluation and selection
Subcontractors play a significant role in the workmanship and quality outcome of your project. To help select quality workers for your project, start by having a subcontractor evaluation and selection process and program in place. Such a program could include:
- Checking their financials, references, project experiences and losses.
- Requiring appropriate licenses and certifications to perform the work.
- Evaluating the subcontractor’s in-house safety and QA/QC written program/procedures.
Contractual risk transfer
Contractual risk transfer (CRT) is a program designed to help protect you against potential liability for the actions, services or products of other companies/persons associated with your project. Consult with your insurance agent and legal counsel for recommendations and review. A few considerations include:
- Written contract of requirements, responsibilities and accountabilities.
- Insurance coverage specifications (auto, general liability, workers comp, etc.).
- Indemnification agreements.
- Current Certifications of Insurance and Additional Insured endorsements.
A quality project
While many companies have a QA/QC program in place, it is only good if it is used. Keeping it updated and documented, selecting the right subcontractors, having contractual risk transfer in place and enforcing accountability for utilization of the program can help make the difference between a quality project and one that has issues, potentially damaging your hard-earned reputation.
Want more? Use your customer ID to access Reducing Construction Defects by Process Control.