Job Site Safety Technology: 5 Things to Consider Before Implementing
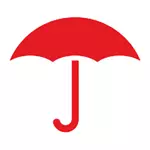
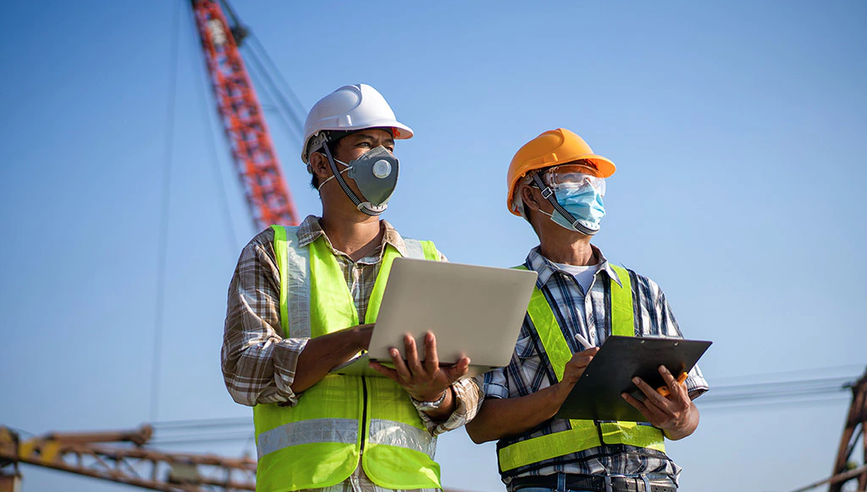
The COVID-19 pandemic has accelerated a digital transformation that is creating smarter, connected job sites. Originally developed to focus on workplace safety and reducing common risks, new applications of job site safety technology, such as proximity sensors, have helped aid contact tracing, and enforce social distancing and other pandemic protocols.
Connected job site technology can be a powerful tool to improve worker safety, both through real-time alerts and by gathering data to be analyzed for potential trends. “More and more devices are being introduced on construction sites that can collect data as well as inform site management about a variety of worksite exposures and worker behaviors,” said Ken Wengert, Vice President of Construction, Energy and Marine Risk Control at Travelers. For example, a wearable device that monitors lumbar motion can gather data to help identify high-risk activities and provide insights to help prevent injuries.
With sprains and strains continuing to be a frequent cause of injury in construction, these types of devices, while early in their development, show significant promise. Our Risk Control Consultants interact with hundreds of customers every week, and as we help customers enhance their risk management programs, we understand that introducing anything new to a workforce can present challenges.
“Workers could be apprehensive about the use of connected job site technology and the data collected,” Wengert said. “Companies should openly communicate with workers on the benefits of the use of connected technology and, also, what data will be collected and how it will be used to reinforce that it is being used to promote safety.”
Here are five considerations before implementing job site safety technology:
1. Consider the Issues You’re Trying to Address
More and more wearable devices and other technologies are being positioned to help the construction industry. Identifying your objectives upfront can help you filter through available technology solutions to help you meet your goals.
“In our experience, a critical element in making technology decisions is to identify what your business is trying to improve or what risks you are trying to reduce,” Wengert said. Just like implementing a new safety or other work procedure, supervisors and workers at construction projects will need oversight to make sure they understand implementation nuances, as well as how to react to data that is produced.
2. Have a Plan for Managing and Interpreting Data
One significant challenge we have experienced with introducing technology into existing operations is that, sometimes, management can be inundated with too much data. As planning takes place, spend time understanding what types of reports will be produced and how they could be used to modify site conditions and/or worker behavior. Some technology vendors have sophisticated dashboards, while others do not. Vetting this upfront can help avoid surprises later. Other considerations include who will have access to the data, how it will be stored and what contractual modifications may be required, such as when general contractors are hiring trade contractors.
Data security is critical as well. Vendors should be asked to explain how they protect customer data, while in their use or in subsequent distribution or sale of that data. Encryption practices and revoving personally identifiable information (PII) are typical tactics among vendors, but data security and privacy should not be assumed.
“Gathering the right data and properly interpreting that data can have a big impact on losses and potential accident costs,” Wengert said. However, avoid trying to adapt on the run and instead, have a well-thought-out plan that includes data collection, the roles and responsibilities for those with access to that data, and specific actions you expect site management to take.
For example, Travelers loss data for construction shows that 38% of workers compensation claims occur with workers who have less than one year of employment. One hypothesis we are testing is whether the rate of these types of injuries will decrease if we drive more supervisor interaction with newer workers. Using technology that shows where workers are working and how often the site supervisor is on-site, real-time alerts can be sent to remind them that more interaction is needed for higher-risk workers.
3. Prepare to Update Safety Training
Potential impacts to your existing training programs should be outlined, including how you expect field supervision to react. “As we have tested technologies in a variety of industries, data will drive downstream changes to what had been a traditional process within a company,” said Wengert. Think about coaching employees where past interactions relied more on visual observation where an unsafe act was quickly addressed. Using data to coach behavior is different, not only for the worker, but for the supervisor as well. Again, upfront planning is critical to the successful implementation of technology.
Also, onboarding practices may need adjustment in terms of incorporating a company’s stance on technology, how it is being used and how it may be included in how a worker is assessed. Leaning on your legal and human resource partners can help avoid employee privacy issues that may arise.
Lastly, we have seen that data can drive changes to conditions on worksites as well. In one case, data showed that at the same time every day, a group of construction workers were showing real-time, low-height alerts. Following a closer review, it was discovered that workers were jumping off an auditorium stage at lunchtime due to lack of other egress routes. Addressing this situation quickly helped workers avoid a potential behavior that over time, could have resulted in injury.
4. Educate on the Value of the Devices
Whether you are a general contractor implementing technology on a construction site, or a company using technology within your own direct workforce, education can help allay potential concerns. For example, some companies and workers may view wearable devices or other technology as an infringement of their privacy. In some cases, you may need to consider adding technology usage into subcontract agreements as well as employee practices. In addition, outlining what the technology being used will measure, how the data will be collected, stored and used and how it is intended to improve worker safety can help increase the chances of effective implementation.
For wearables devices to be effective, they require consistent and proper use. Wengert likens the advent of wearable technology to the introduction of the seat belt in the automobile. “You still had to have the driver put the seat belt on for it to be effective, and now, at minimum, workers need to be coached to not only use the wearable [device], but use it correctly in order for it to be effective,” Wengert said.
While we have seen some technology/wearable adoption go well, we have also seen some fail. One key theme for success is the need to designate someone in your organization to be accountable and responsible for implementing technology. Without this type of ownership, we have seen implementation slow, and in some cases stop, since no one individual is overseeing the elements we have discussed thus far.
5. Work with an Experienced Carrier
In our work with technology/wearable vendors, we have helped bridge a gap between vendors who may have limited industry or insurance experience and our customers, who may have limited experience introducing technology/wearables into their workforce or job sites.
“We meet with several thousand contractors each year,” Wengert said. “We not only share industry insights and assist in analyzing job site risks, we also share our insights about connected technology and how these products and services can be used to help them address these risks.”
Working with a carrier like Travelers, which has hundreds of underwriters, claim professionals and Risk Control Consultants throughout the country dedicated to the construction industry, can be an asset in implementing new technology.